3 Metal Parts Contaminating Plastic Waste
By Paul Fears | 04 June 2020
Recycling plastic waste is challenging at the best of times. However, when contaminated with ferrous metals, recycling is hindered by equipment damage, production downtime and poor end product quality. Thankfully, installing the optimum magnetic separator ensures that such ferrous metal contamination is removed. In this article we look at three examples of ferrous metal contamination successfully separated in a UK plastic waste recycling plant.
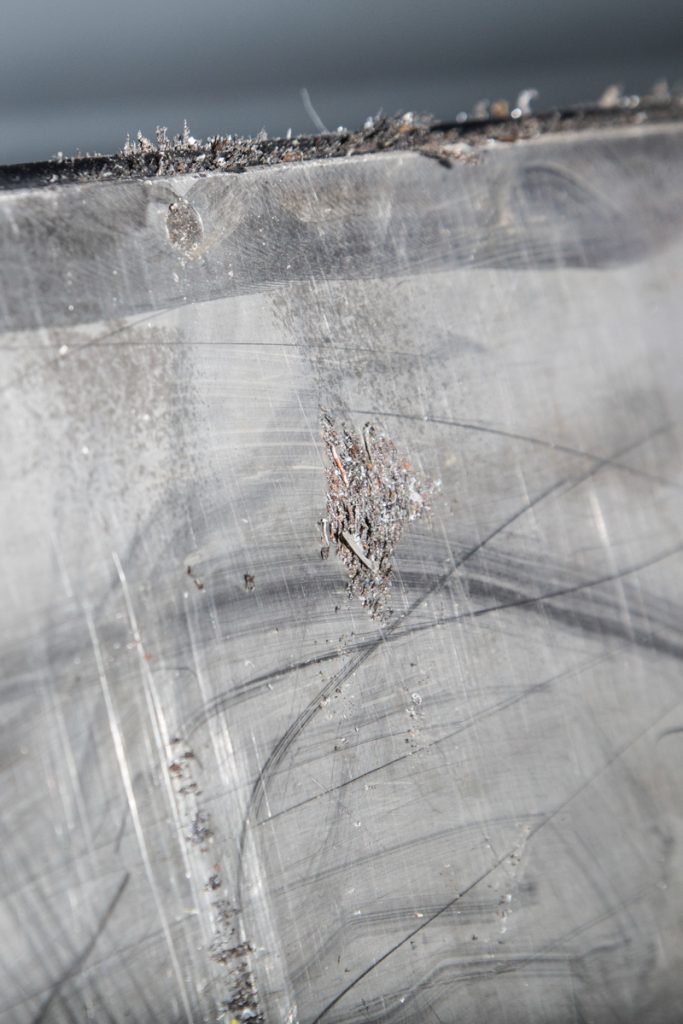
Fine Metal Shards and Dust
The metal found on the face of this ultra strong Rare Earth Plate Magnet is quite fine and has been lifted up out of conveyed material. Fine iron is difficult to separate, causing significant wear to plant and also contaminating the final product. In this particular installation, Plate Magnets were used both suspended above conveyors and positioned in chutes (where material flows over the magnet face). In some installations, fine iron is automatically removed using Permanent Drum Magnets which also provide continuous and maintenance-free operation.
- Product details: Rare Earth Plate Magnet
- Product details: Permanent Drum Magnets
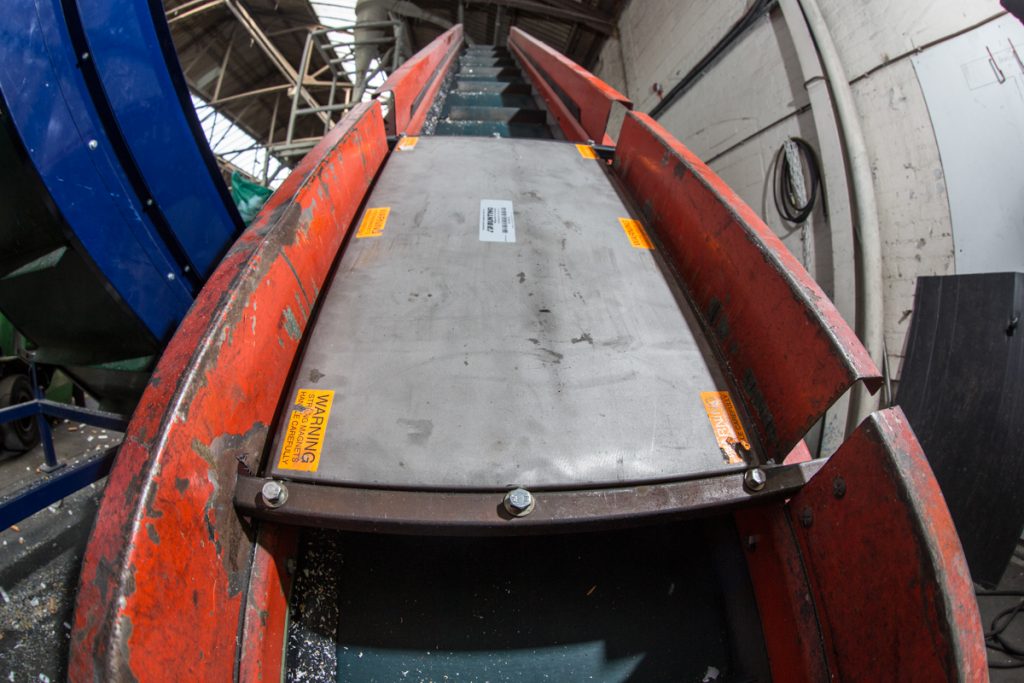
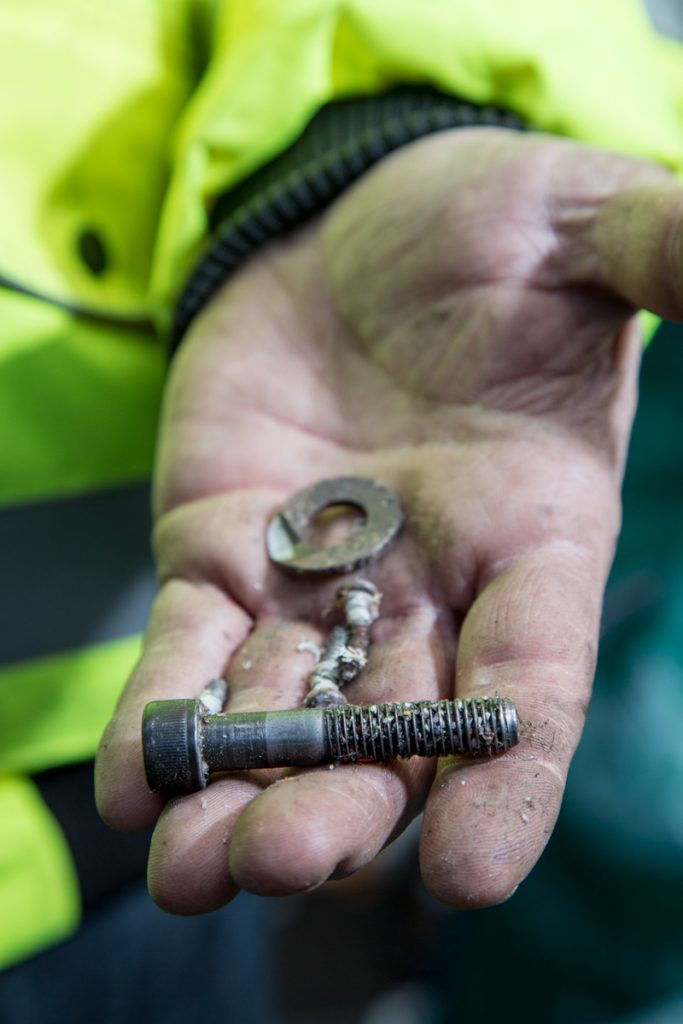
Nuts, Bolts and Screws
Nuts, bolts and screws are more typical examples of metal contamination either present in the delivered reclaimed plastic or introduced into the process from plant wear or during maintenance. Such metal contamination causes significant damage to process plant and is costly in terms of equipment repair and production downtime. In this plastic waste recycling installation, this type of ferrous metal contamination was removed using a Magnetic Head Pulley. The Magnetic Head Pulley replaced the head pulley of a conveyor. The plastic waste is conveyed into the magnetic field of the Magnetic Head Pulley, which attracts and holds ferrous metal contamination, depositing it underneath the conveyor and out of the main product stream.
- Product details: Magnetic Head Pulley
Large Spanner
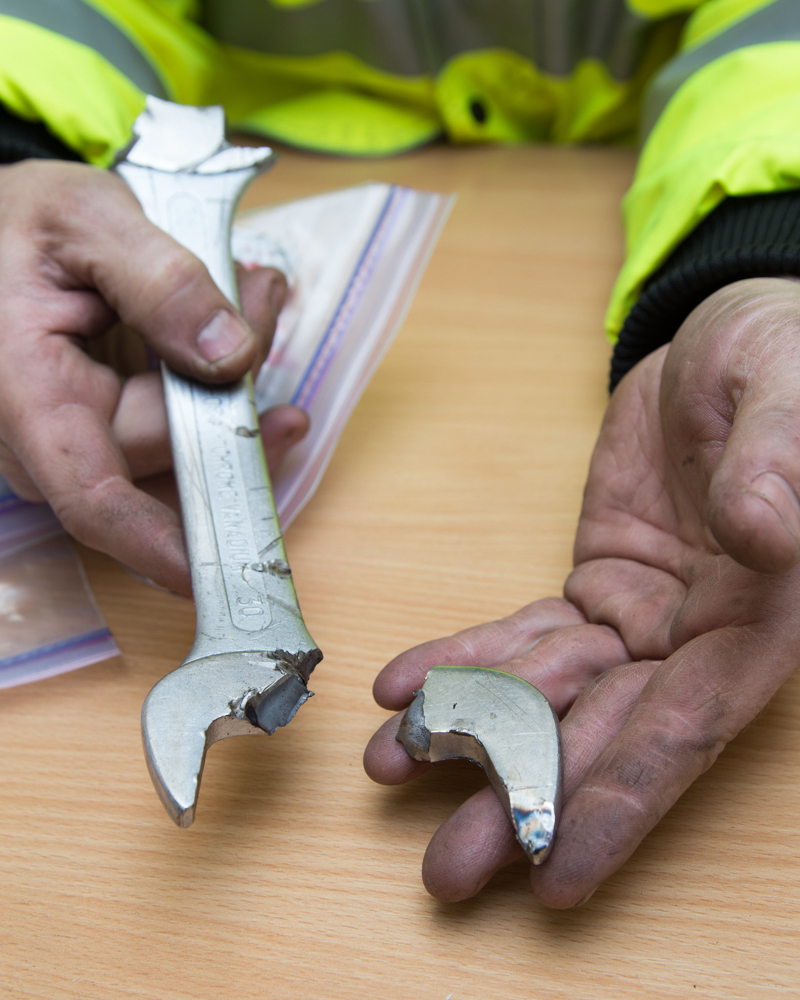
An extreme, but not unusual, example of metal contamination is a large spanner. The damage that a tool causes is significant in terms of cost and plant downtime. Introducing a spanner into a shredder or granulator often has disastrous consequences. The spanner in this photograph was separated using a Magnetic Head Pulley. Depending on the plant layout, such large ferrous metal contamination is also separated using a Drum Magnet or Overband Magnet.
- Product details: Overband Magnet
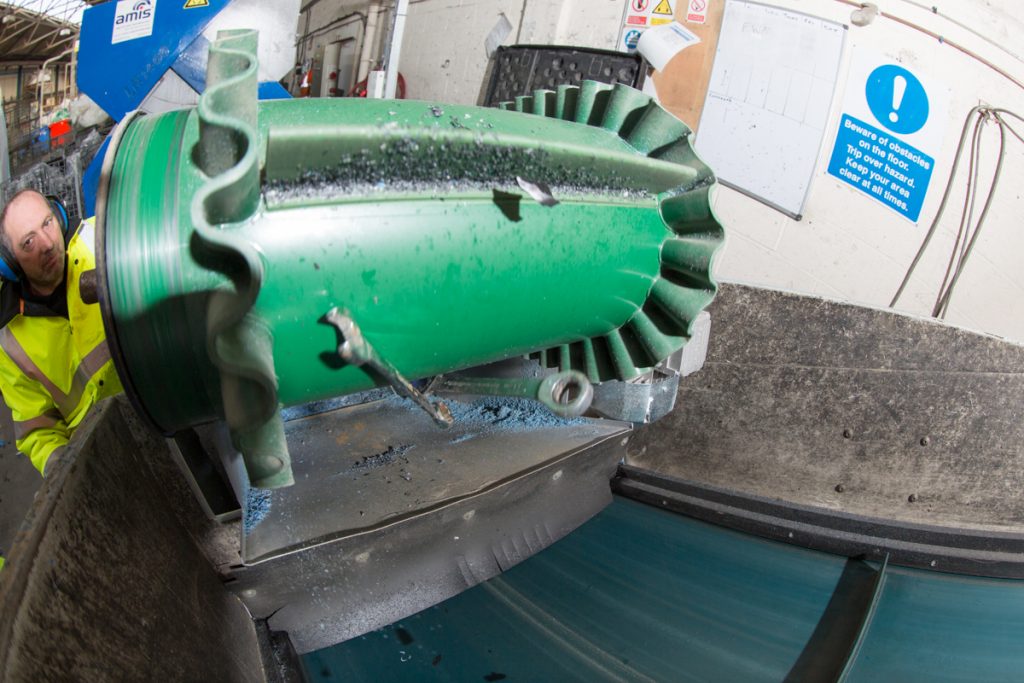
Total Metal Separation Solution
Other plastic waste recycling operations also use Eddy Current Separators (to remove non-ferrous metals such as aluminium) and Metal Detectors (to identify large and small metals). The right combination of metal separation equipment is dictated by the process. Commonly, Bunting engineers attend site to assess the optimum locations and type of equipment to solve a metal contamination problem.
Relating Recycling Articles
- Bunting Secures Major Export Recycling Equipment Order
- EcoVyn Reduce Plastic Waste by 94% with Bunting
For additional information on removing metal from plastic waste or to arrange an onsite review, please contact us on:
Email: Gordon Kerr at GKerr@buntingmagnetics.com
Telephone: +44 (0) 1527 65858
Follow us on social media