Separation Challenges of Recycling PET for Plastic Bottles
By Paul Fears | 30 October 2023
Article first published by Powder and Bulk Solids (August 2023)
Raw material shortages are increasing, and as consumption rises, the gap grows wider. It took a pandemic to open the eyes of most producers as to how fragile the supply chain is. Yet, many powder and bulk operations could do more to alleviate the shortage issue.
There are several reasons as to why there may be a material shortage. Some are controllable, and some are simply beyond our control. Within the powder and bulk industry, shortages can happen with materials coming in from suppliers and going out to customers. Either one could be disruptive enough to put a company out of business.
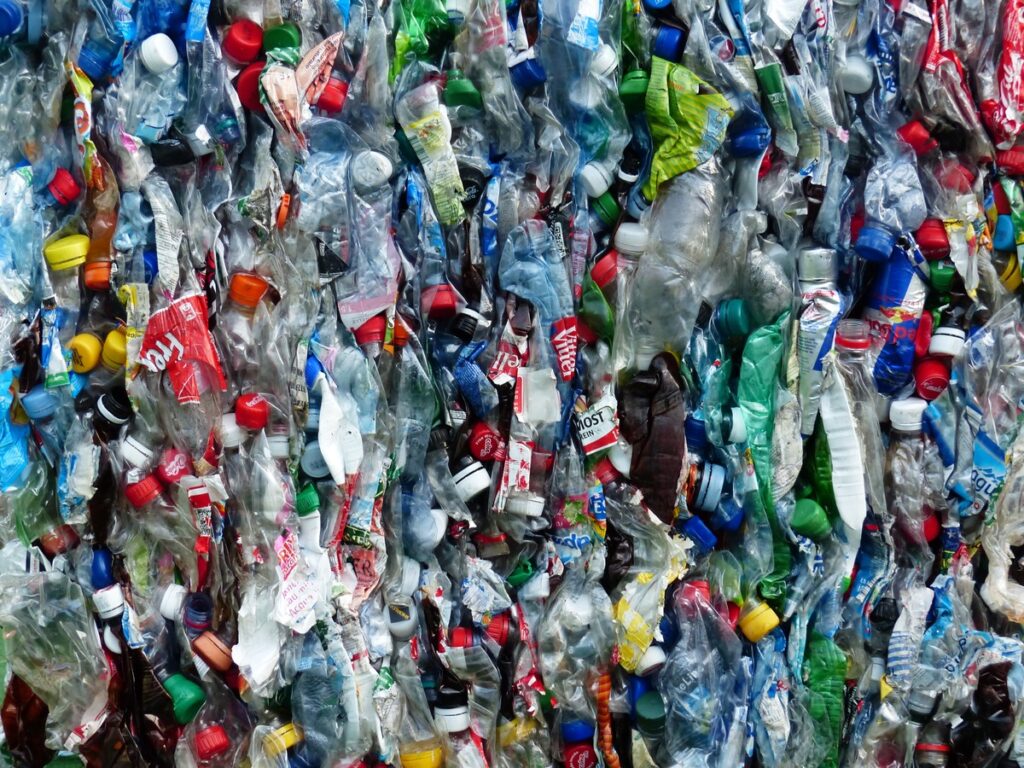
This article will focus on increasing the use of recycled raw materials and, more specifically, recycled plastic water bottles (rPET). When it comes to sustainability, no other industry gets the scrutiny that the plastic water bottle gets. Plastic recycling starts as a dirty process in the municipal recycling facility (MRF). There, various items are sorted manually and mechanically, with a heavy emphasis on plastics. Plastic bottles are split and baled for transport to a plastics recycling facility. There, the bales are broken apart, and the bottles are sorted between clear and green. The sorted plastic is then sent into a shredder or grinder that reduces the bottle into plastic flakes or pellets, and, as in most any grinding or shredding process, there will be some metal contamination that is commingled with the rPET.
Removing Magnetic Contamination
Magnetic separators do a great job of effectively and efficiently removing ferrous metal contaminants with absolutely no loss of product, or at least no loss that wasn’t preventable. Magnets physically hold the ferrous metal contaminant until it is removed or stripped off the magnet either manually or mechanically. With today’s high-strength neodymium magnets, there is no reason any ferrous metal contamination should make it past the magnetic separator.
What About Non-Ferrous Metal Contamination?
What about the non-ferrous metal contaminants like stainless steel or aluminium that are non-magnetically receptive? The best choice for removing these particles is to use a metal detector, like a quickTRON 03 Metal Detector, in combination with some reject mechanism. Reject mechanisms can be programmed to operate efficiently. Still, no matter how efficiently they are programmed, some non-ferrous metal particulates will make it through the reject process. The orientation of the contaminant within the rPET flake, the size of the contaminant, and the settings on the metal detector all play a part in catching the contaminant. For all practical purposes, we might say the rPET is 92% clean of metal contamination.
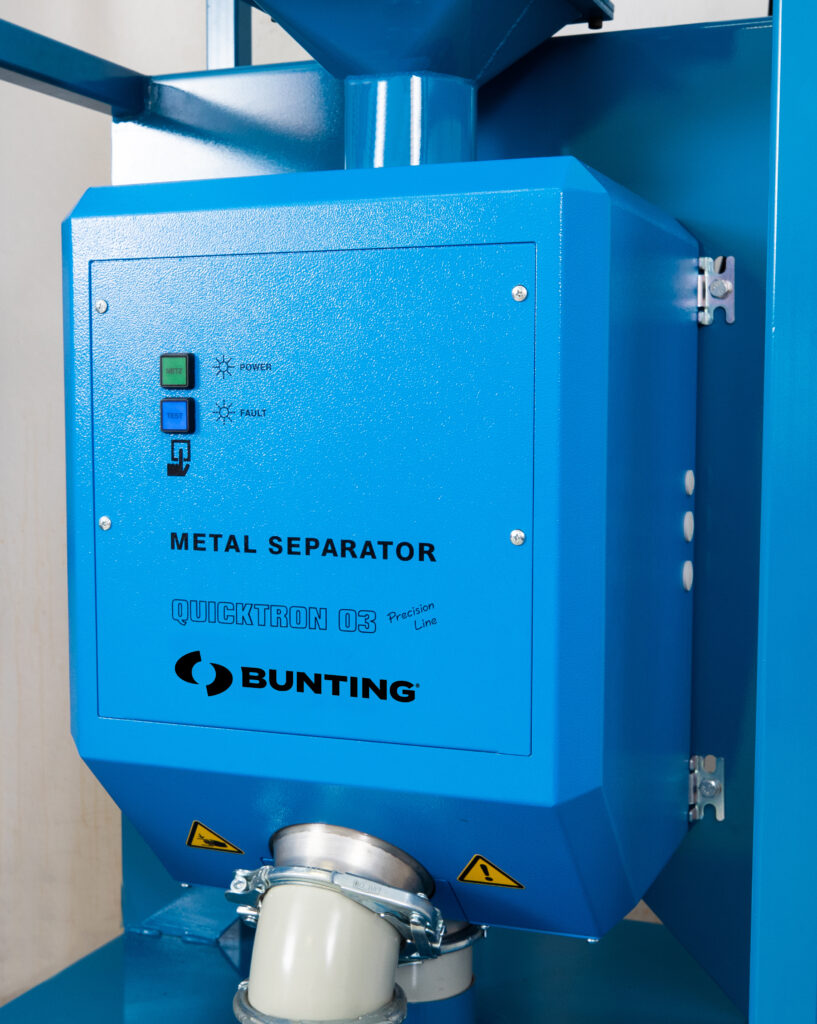
These Bunting QT03 metal detectors are part of a six-lane cascade for recycling PET bottles.
So, 92% may sound good to the recycler, but the bottling company that is looking to buy that rPET needs it to be 99.9% free of any metal contamination. After all, the rPET is a ground-up plastic bottle that will be remade into another. What bottling company would want to risk having a consumer find a shard of stainless steel from a shredder blade embedded in the bottom of their water bottle?
To salvage a rejected bottle that is recycled into material used to make a new bottle is a complicated process that requires a highly purified recycled product. Today, we are seeing a growing trend in the use of a waterfall stack of quickTRON 03 Metal Detectors to remove metal contaminants from rPET. As more plastic flake/pellet material from plastic bottles gets recycled into new plastic bottles, the need for purity is magnified. How is that accomplished? Let’s say that the recycler can reject 92% of metal contaminants with one pass through a metal detector. That 92% pure rPET then gets passed through a second time, which increases the catch rate to 96%. Then, through a third time for a 98.9% catch rate. Each additional pass results in a small amount of rejected material loss, but the purity level of the rPET that has made it through the system is nearing the targeted purity rate of 99.9% metal-free that the bottling company has specified.
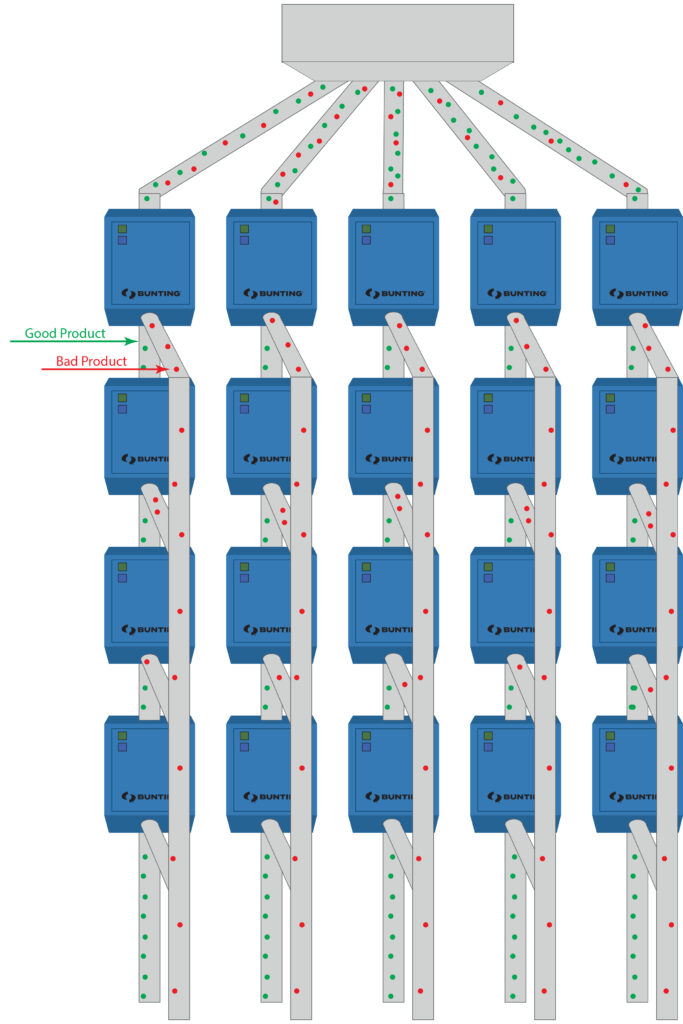
Sounds slow, repetitive, and expensive. It does not have to be with a system designed for that specific purpose. By stacking multiple metal detectors on top of the next, the purity rate of the product flow is improved mechanically. But will multiple metal detectors for that purpose generate a reasonable payback? That depends on the flow rates, the types of metal detectors, and what level of monitoring needs to be done. If the flow rate going through the detectors is significant, say at the level required to supply 30, 40, or 50% of the PET needed by an injection moulding operation to make the parison blow moulding or “pre-forms” the bottling plant needs, that is a significant amount of plastic that does not end up in landfills or polluting our natural resources. Is there really a market for that much rPET that came from a used PET bottle? As mentioned before, the sustainability of plastic bottles is under fire today from all directions as consumers push for a sustainable package.
PET bottles are here for the long run, but the pressure from consumers, ecologists, and environmentalists to make PET bottles more sustainable packaging is growing rapidly. There exists a market for clean rPET today, but the initial collection channel through municipalities is strained due to labour costs and availability constraints. Some markets have become driven by the concept of reusing PET bottles to make new PET bottles one-for-one, and those markets have instituted a variety of deposit return schemes (DRS) to get sorted bottles returned for recycling. In some countries, even the bottling companies have created their own DRS. In the US, there are currently ten states that have implemented “bottle bills” that cover plastic bottles and the “Container Recycling Institute” has a “Bottle Bill Resource Guide” at www.bottlebill.org.
It should be noted that no national bottle bill exists in the US. But there are multiple efforts to pass legislation, and it is just a matter of time before a national plastic bottle program gets enacted. When such a program exists, the market for recycled PET bottles will have a clean and steady supply. It will be up to the recycler, who turns the bottles into flakes/pellets to meet the standard for separation established by the bottler.
If you are a processor of recycled PET content and you would like to see whether you could benefit from a stacked system of metal detectors, run a test on your equipment by repeatedly recycling your raw material through your metal detector, weigh and track the volume of metal contamination with each successive pass until you reach your own established target level. You can verify your results by sending a similar sampling of the raw material to your OEM for testing. You can even ask for a live demonstration.
Related Recycling Articles
For further information on Metal Detectors, Magnetic Separators, Eddy Current Separators, and ElectroStatic Separators for metal separation in recycling applications or to discuss a specific project, including undertaking tests in our Customer Experience Centre, please get in touch with our technical sales team on:
Email: Michael Allen (mallen@buntingmagnetics.com)
Telephone: +44 (0) 1527 65858
Follow us on social media