EMR Team’s Metal Separation Training
By Paul Fears | 10 August 2022
A team from leading European metal recyclers European Metal Recycling (EMR) visited Bunting’s Customer Experience Centre in Redditch, UK to see demonstrations on the latest metal separation equipment. The team included students, new employees, and a research and development engineer.
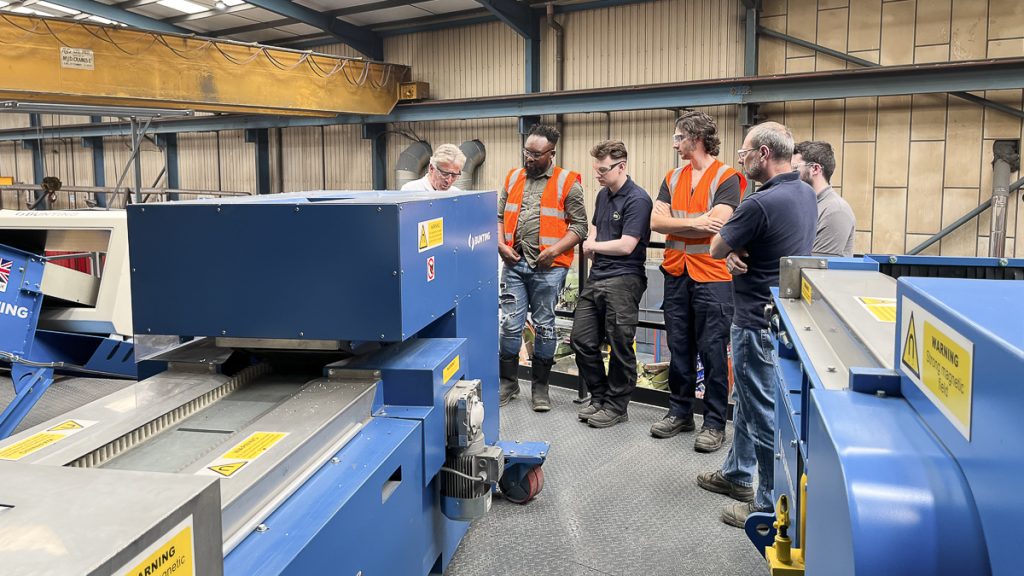
EMR is a global leader in the management of sustainable materials, investing in cutting-edge technology and world-class research with a dedicated team of recycling experts. With facilities across the globe and a team of over 3,000 people, EMR’s operations put 10 million tonnes of material back into the supply chain annually. The latest visit follows the training of EMR students in September 2021.
Understanding Metal Separation Possibilities
Bunting’s Laboratory Manager, Neil Rowson and Sales Manager, Phil Tree demonstrated a wide range of separation technology used in the recycling sector and for the purification and concentration of minerals. Neil Rowson has over 35 years of experience in material separation, including a professorship of Chemical Engineering at the University of Birmingham. Over the past 40 years, Phil Tree has helped companies solve material separation problems with a wide range of magnetic technology.
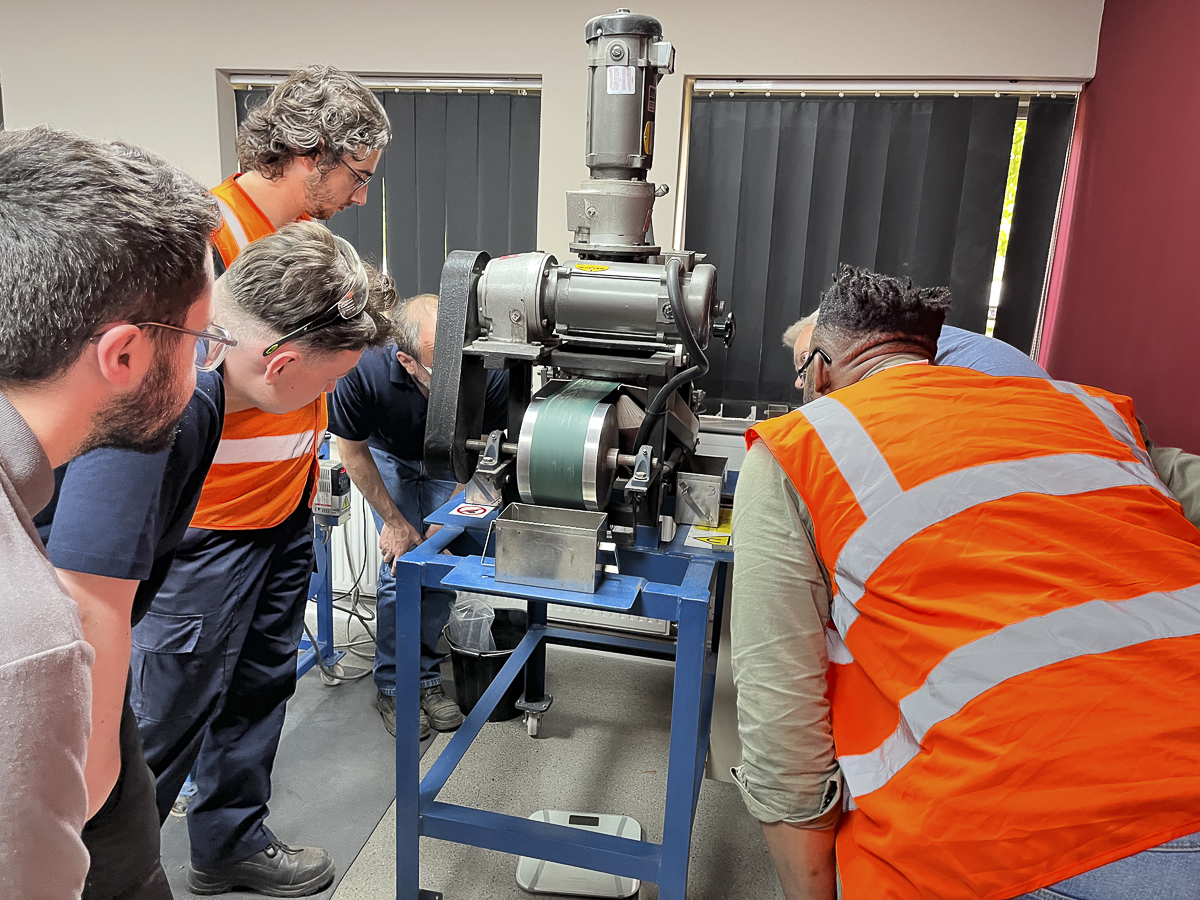
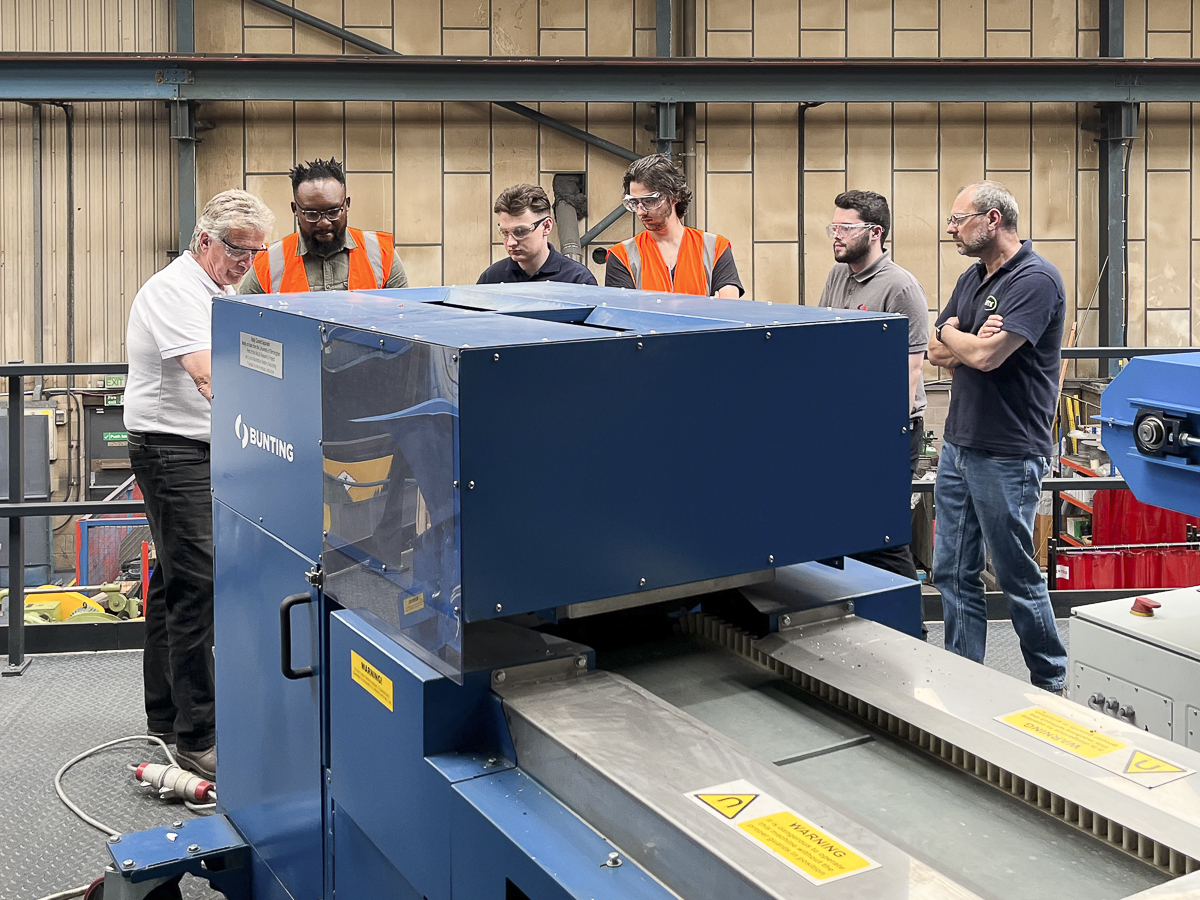
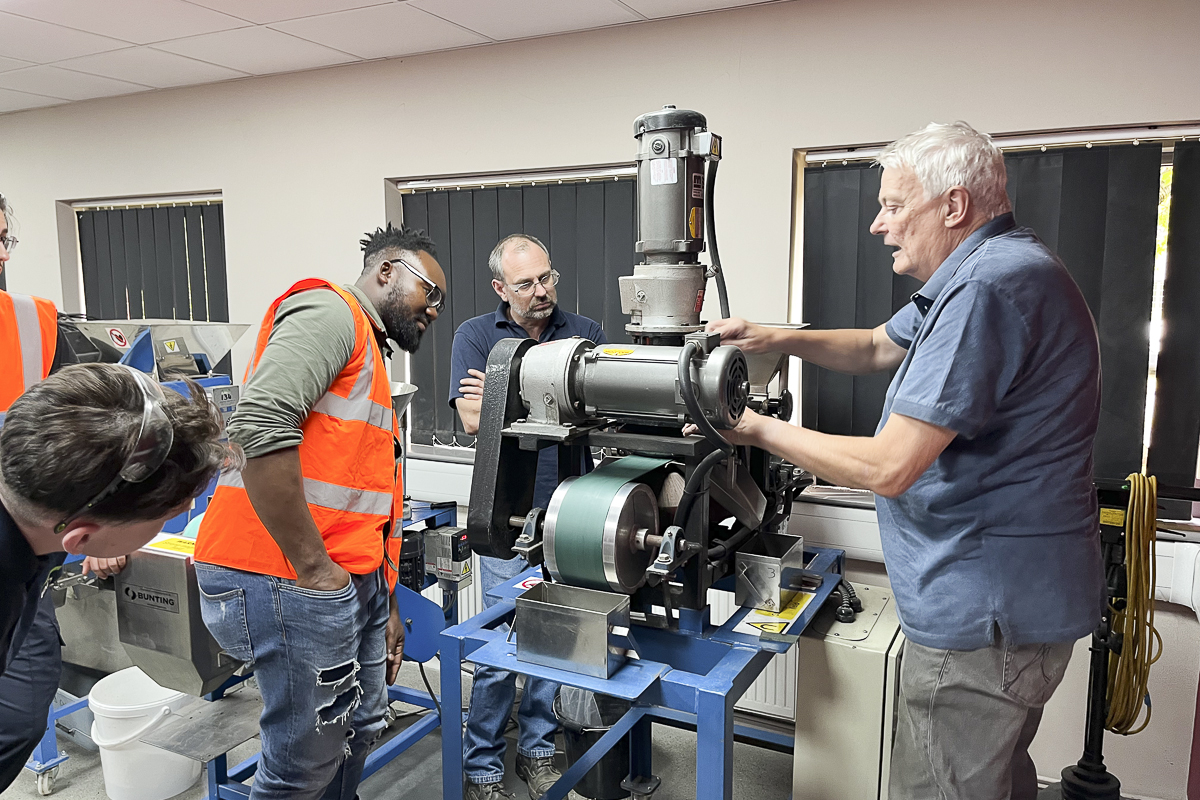
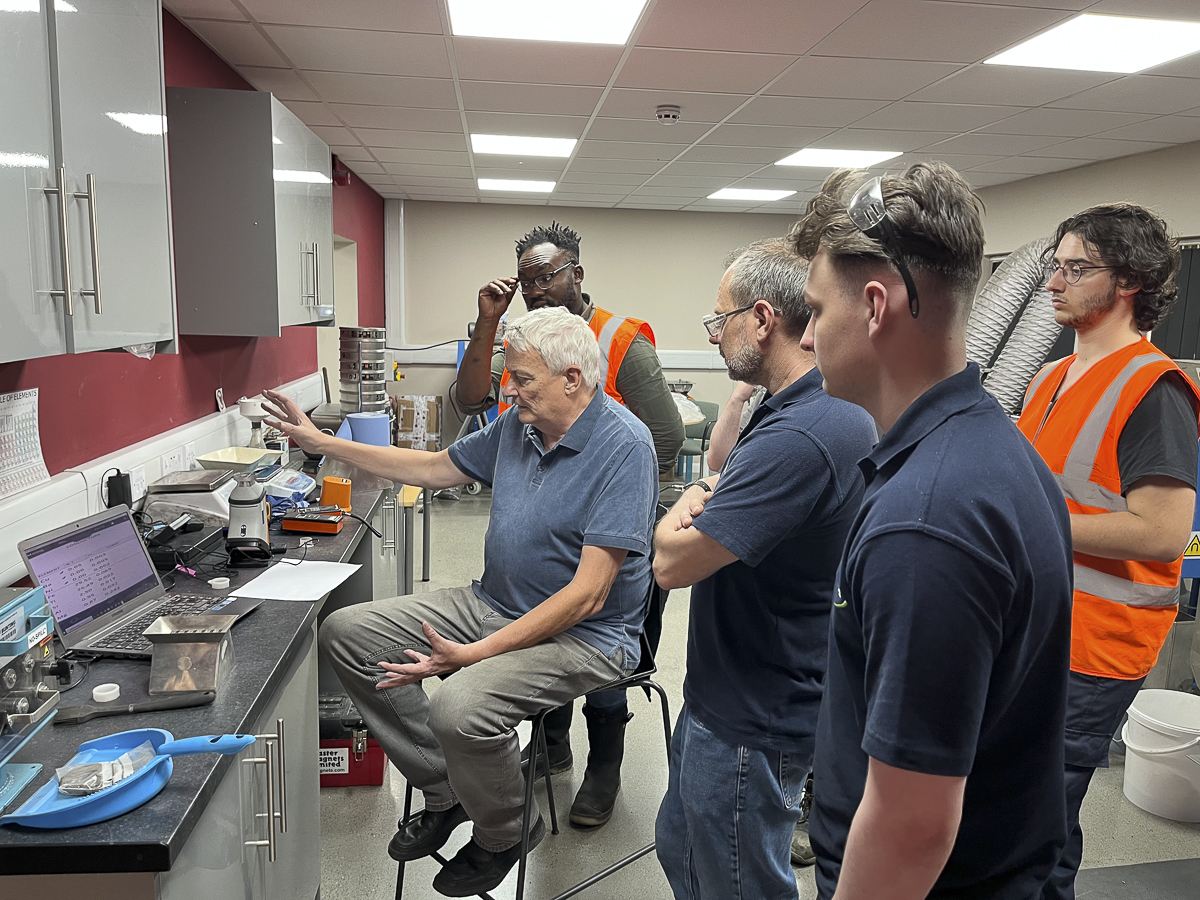
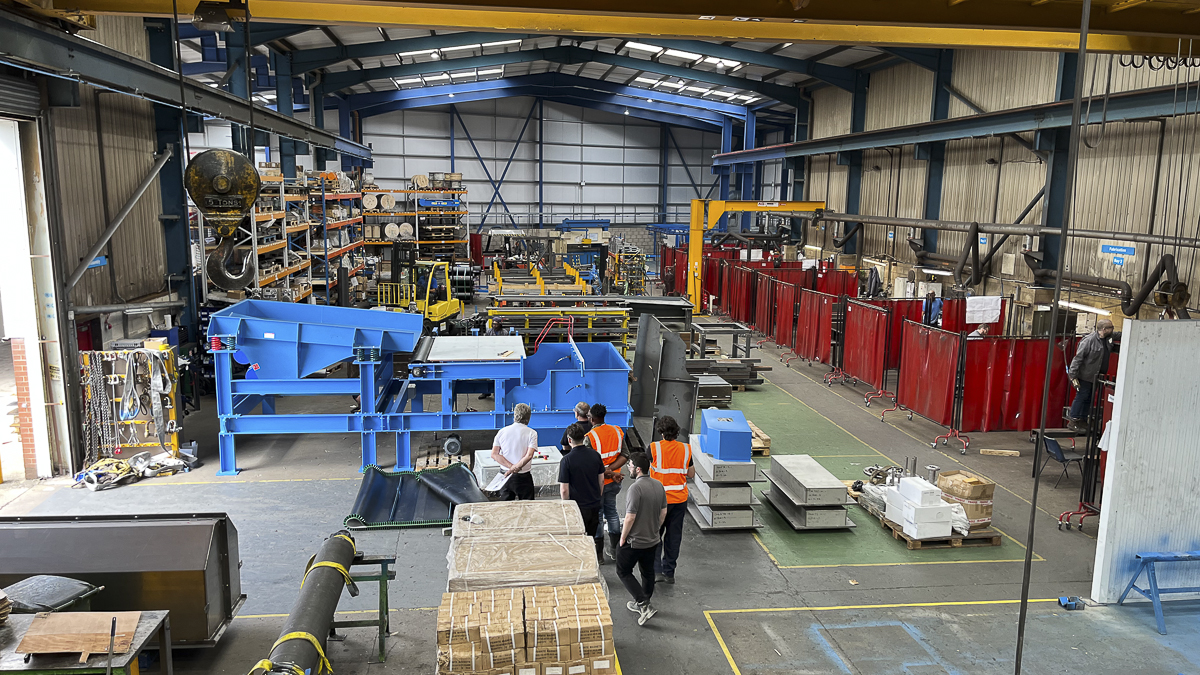
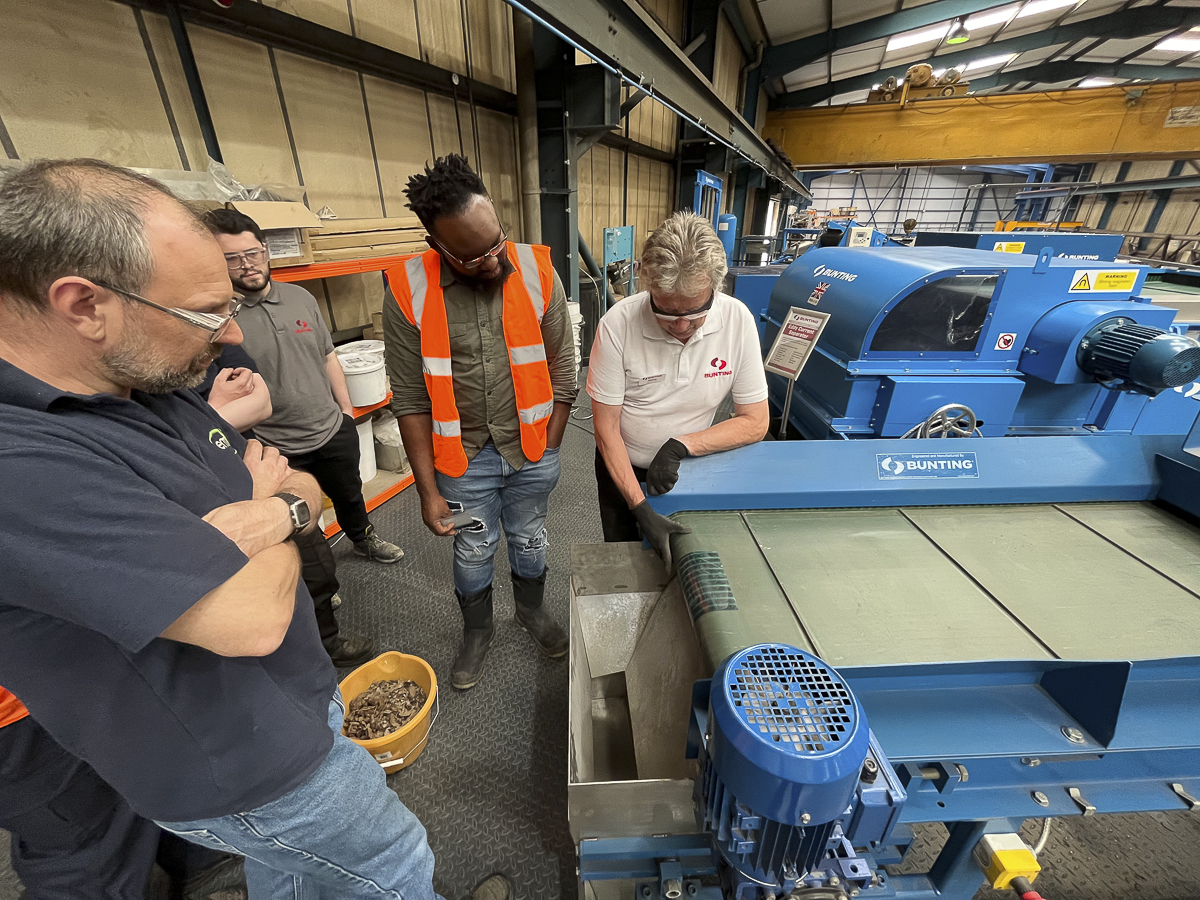
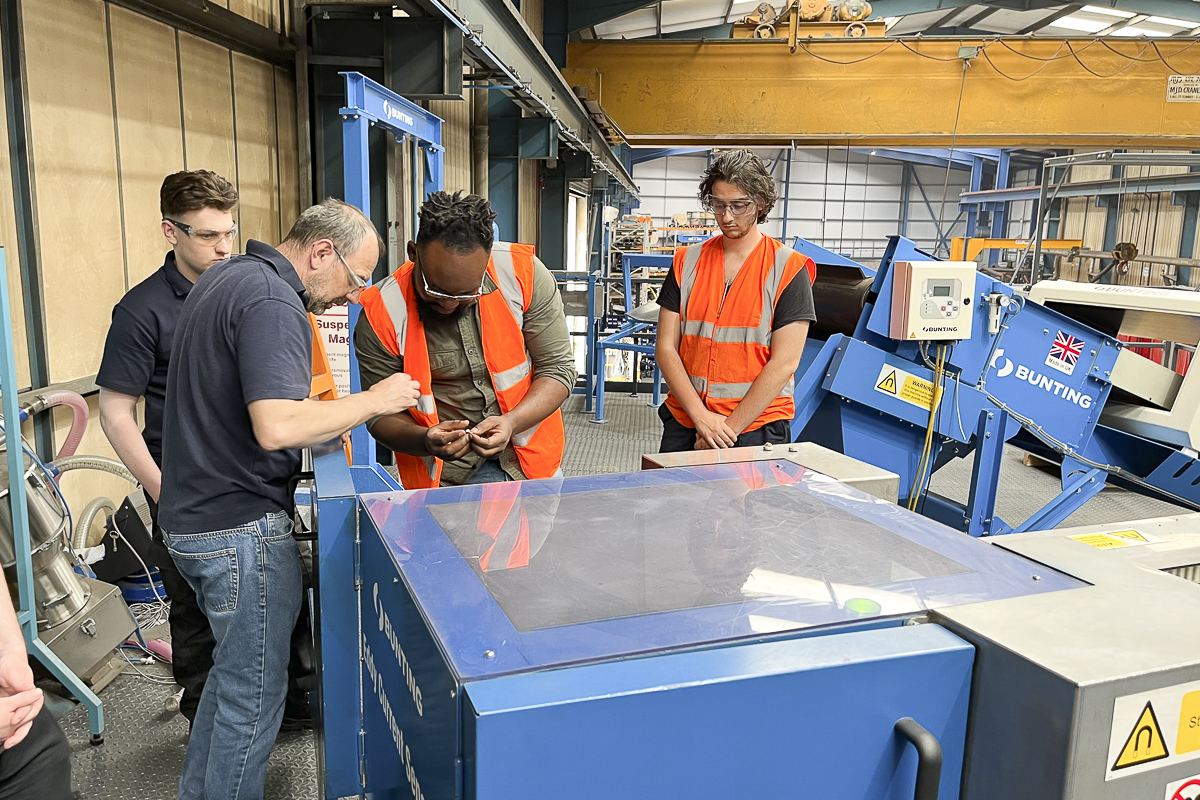
As EMR and other metal recyclers look to increase recycling rates and reduce waste, there is a growing demand for the recovery and separation of smaller particle metals. During the training visit, the EMR team was shown how a multi-stage separation process enables the optimum recovery of smaller metals.
A typical system, similar to that supplied for the recovery of small aluminium from crushed dross, includes:
- High-strength Rare Earth Drum Magnet to remove fine ferrous materials;
- An Eddy Current Separator for recovery of smaller aluminium;
- An ElectroStatic Separator that recovers finer aluminium unrecoverable on the Eddy Current Separator;
The three-stage metal separation process increases metal recovery and reduces waste.
The EMR team was also shown the ability of the SSSC and HISC Stainless-Steel Magnetic Separators. The patented high-intensity magnetic head rolls produce field strengths to recover weakly magnetic materials including fragmented stainless-steel and printed circuit boards.
Equipment Suppliers and Recyclers Working Together
EMR and Bunting are working together on a number of projects. Understanding the challenges faced by a metal recycler enables Bunting’s development team to assess potential metal separator improvements and innovations.
“Having the EMR team at our Customer Experience Centre helps us understand the challenges they face,” explained Neil Rowson, Bunting’s Laboratory Manager. “We are privileged to provide training for EMR employees new to the recycling industry and those who are responsible for development.”
Related Recycling Articles
For further information on Magnetic Separators, Eddy Current Separators, and ElectroStatic Separators for metal separation in recycling applications or to discuss a specific project including undertaking tests in our Customer Experience Centre, please contact our technical sales team on:
Email: Gordon Kerr at GKerr@buntingmagnetics.com
Telephone: +44 (0) 1527 65858
Follow us on social media