New Powder Coating Plant at Bunting-Redditch
By Paul Fears | 05 July 2021
The newly refurbished and extended Bunting-Redditch facility now includes a new powder coating plant. Powder coated painting produces a top quality finish and further enhances Bunting’s manufacturing standard.
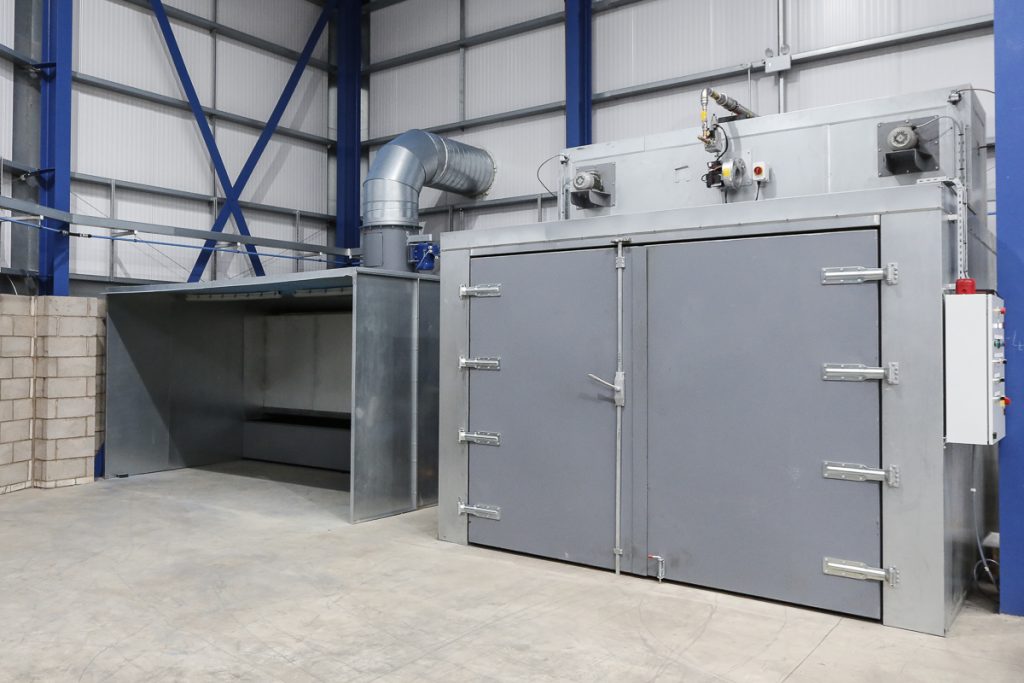
The Powder Coating Plant, installed by PB Metal Finishing Engineers, includes a gas-heated, air-circulated box oven; a water wash booth; a powder machine; and control panel assembly. The complete plant fits in an area of approximately 10 by 6 meters.
Continual Manufacturing Improvement
Powder coating provides better performance than wet paint, being more resistant to chipping, scratching, and other such wear. This is due to the thermal bonding undergone during curing, and the ability to apply in thicker layers. The enhanced paint performance perfectly suits the arduous environments of the recycling, mineral processing, mining, and plastics industries.
The Box ‘Batch’ Oven and Water Wash Booth are self-contained, free standing, and required no floor excavations or special floor preparations. The Oven has galvanised steel folded panels, with between 75mm and 150mm thick thermal insulation, and is designed for 100-400° C operating temperatures.
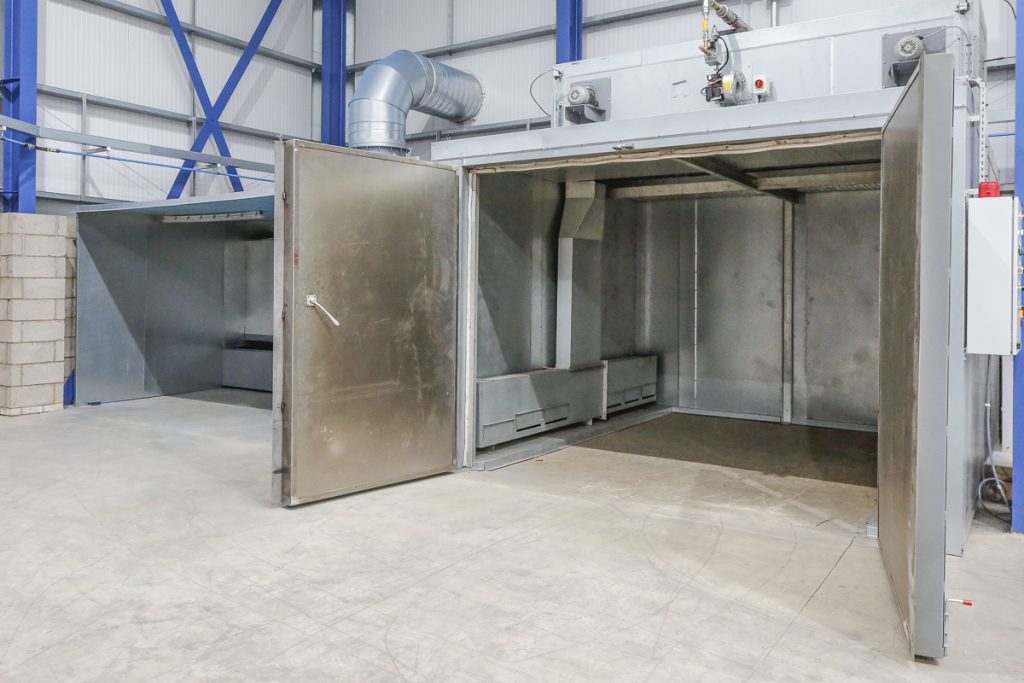
The water wash booth also has galvanised steel folded panels, with the base formed by a heavy welded steel tank, protected, painted and complete with metal mesh filters, water level control valve and drain valve. The bottom roof is steel framed and sheeted, self-supporting and with glazed panels for external fluorescent lights. The continuously flushed rear flow plate is in stainless steel. Behind the screen is a scrubbing chamber with moisture eliminator banks in the upper portion accessible through lift off covers.
The single, floor-mounted control cabinet operates and monitors all the electrical functions of the plant. The sheet-steel control panel is dust and damp protected to IP54, with gland plates fitted for cable entry in the base of the panel.
Separators Operating in Harsh Environments
Separation equipment commonly operates in the harshest of environments with Eddy Current Separators in recycling operations, Overband Magnets in mines and bulk handling terminals, Magnetic Disc Separators in mineral processing plants, and Drawer Filter Magnets in plastics manufacturing.
“The extension to the Redditch facility provided the ideal opportunity to improve parts of our manufacturing process,” explained Adrian Coleman, the General Manager of Bunting-Redditch. “Installing this powder coating plant significantly improves the finish of our separators and is ideal for many of the harsh working environments in which our equipment operates.”
Related Company News
For further information on Magnetic Separators, ElectroStatic Separators and Metal Detectors or to discuss a specific project including undertaking tests in our Customer Experience Centre, please contact our technical sales team on:
Email: Gordon Kerr at GKerr@buntingmagnetics.com
Telephone: +44 (0) 1527 65858
All photography by Paul Fears Photography
Follow us on social media