Metal Separation When Recycling UPVC Windows
By Paul Fears | 30 March 2022
353,000 tonnes of window profiles and related products got recycled in 2020 (source Recovinyl). Although there was a slight fall in the total amount of PVC recycled in 2020 (due to the Covid-19 pandemic), the UK and Ireland recycle the second highest tonnage in Europe behind Germany.
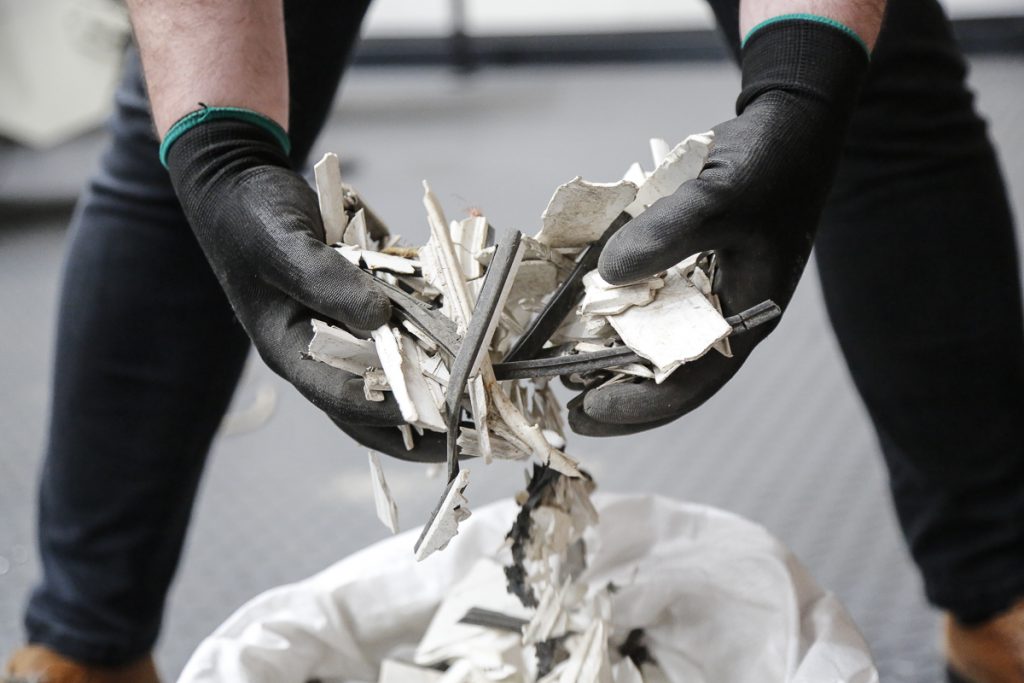
The recycling of UPVC windows is a long-standing success story. Since the early 1990s, changes in window and profile designs aided the recyclability, making separation of individual components and materials easier. And metal is a key material to remove.
There are many metal components in a UPVC window including handles, hinges, and locks. These could be steel, stainless-steel, aluminium, and brass. If such metal is not successfully removed during the recycling process, it can cause serious and costly damage to process equipment (e.g. shredders) and reduce the value of the end resaleable product.
Removing the Metal
The metal present in UPVC windows is a mixture of ferrous (magnetic), non-ferrous (non-magnetic) and stainless-steel (weakly magnetic post shredding). This means the necessity of several stages of metal separation, using different metal separation technology.
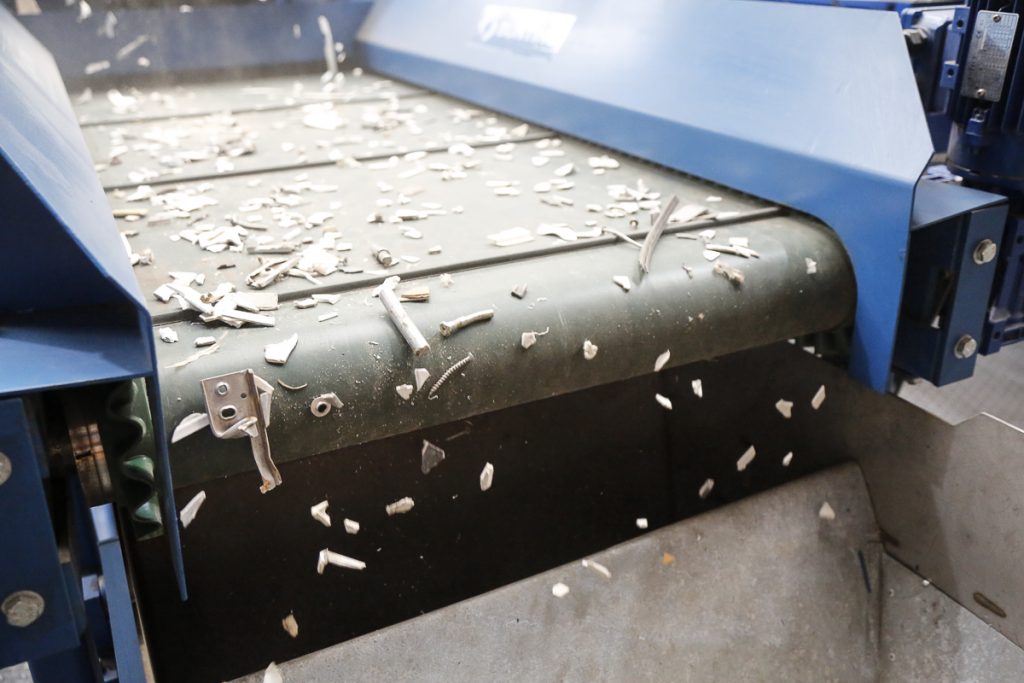
Optimum metal separation is a function of the liberation of the metal from the plastic and the performance of the magnetic separation equipment. After the UPVC windows are manually separated into white and non-white, a primary stage of shredding produces a coarse fraction containing free larger metal. At this stage, there are two options for ferrous metal extraction.
Ferrous Metal Separation
An Overband Magnet consists of a magnet block (permanent or electro) mounted between two pulleys over which runs a belt. The Overband Magnet sits over the shredder discharge conveyor, lifting and automatically depositing ferrous metals into a separate collection area. Successful ferrous metal separation replies on a thin layer of conveyed material, reducing the chance of obstruction as the metal is pulled up and towards the magnet face.
- Technical product details: Overband Magnets
The Drum Magnet commonly produces a higher level of ferrous metal separation. In operation, an even layer of shredded material feeds onto the top surface of a rotating non-magnetic shell. Inside the rotating shell is a stationary arc of magnets. Magnetic materials in the feed are attracted by the field and deposited underneath the drum away from non-magnetic materials. The field intensity on the surface of the Drum is higher than the force generated by the Overband Magnet, which can result in higher levels of ferrous metal removal.
- Technical product details: Drum Magnets
Non-Ferrous Metal Separation
Eddy Current Separators automatically eject non-ferrous metals from non-metallic materials. A high-speed rotating magnet rotor mounted inside a non-metallic shell operates as the head pulley on a short conveyor system. A vibratory feeder delivers an even layer of material onto the conveyor, which is then transported onto the head pulley and into the rotating magnetic field. The alternating magnetic field generates a current in the non-ferrous metal, producing a magnetic field which is always in opposition to the rotating field. This causes the metal to repel, with a strategically placed splitter ensuring capture and segregation away from the remaining material.
- Technical product details: Eddy Current Separators
Stainless-Steel Separation
Until recently, the effective extraction of stainless-steel was difficult. Stainless-steel passing through a shredder becomes weakly magnetic, but the magnetic susceptibility is too low for successful separation using other magnetic separators such as Overband Magnets.
The HISC and SSSC Magnetic Separators use an ultra-high magnetic head pulley to separate very week magnetic particles. In operation, a vibratory feeder delivers a mono-layer of material on to thin conveyor belt. The belt moves the material into the magnetic field of the head pulley, where the attractive force of weakly magnetic particles alters the material trajectory and enables separation from non-metallic materials.
- Technical product details: Stainless Steel Magnetic Separators
Metal Detection
Passing the UPVC through one or two stages of Metal Detection identifies any small amounts of remaining metal, especially embedded inside non-metallic materials.
After the Stainless-Steel Separator, the 20-50mm size-fraction feeds through a gravity-fed metal detector, which identifies and automatically rejects any remaining metal contamination. Some plants also have a highly sensitive tunnel-type Metal Detector mounted around a conveyor as a final quality check prior to bagging or storage.
Technical product details: Metal Detectors
UPVC Ready for Reuse
After the separation of all metals and further colour recognition and removal, the UPVC is commonly further size-reduced into re-useable granules or powder.
UPVC windows can be recycled at least seven times without having any impact on the quality or weather resistance characteristics.
Related Recycling Articles
For further information on Magnetic Separators, Eddy Current Separators, and ElectroStatic Separators for metal separation in recycling applications or to discuss a specific project including undertaking tests in our Customer Experience Centre, please contact our technical sales team on:
Email: Gordon Kerr at GKerr@buntingmagnetics.com
Telephone: +44 (0) 1527 65858
Photographs and video taken by Paul Fears Photography
Follow us on social media