Two SSSC Magnetic Separators Ordered
By Paul Fears | 24 August 2020
A UK metal recycling company has ordered two (2) SSSC Magnetic Separators to recover fragmented stainless steel.
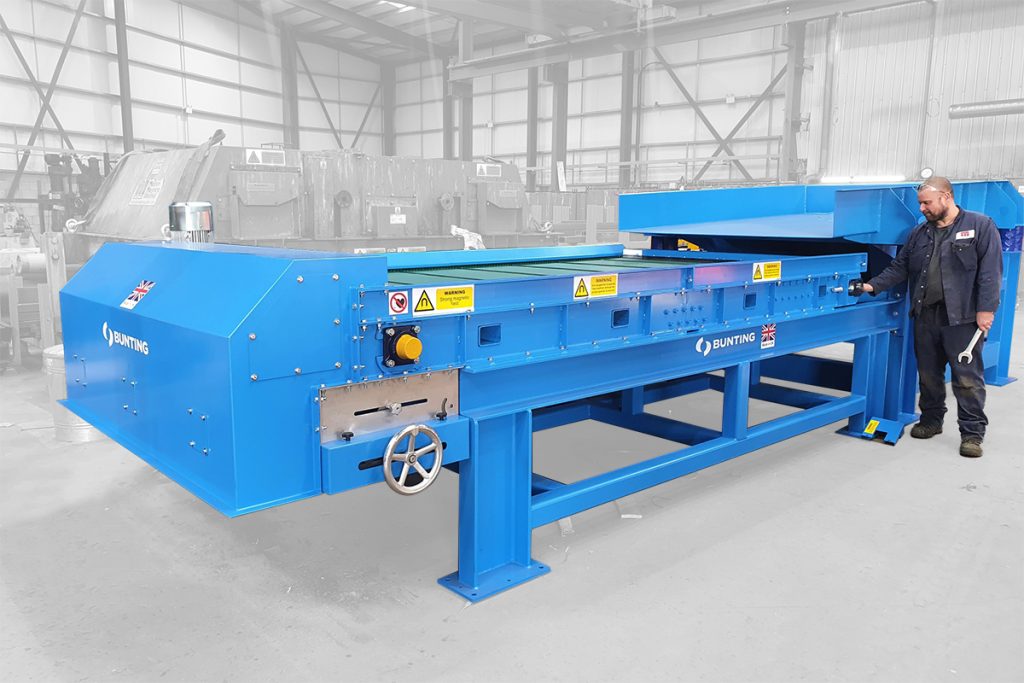
The order followed initial tests undertaken on site with a Rare Earth Drum Magnet during the Covid-19 lockdown. Once the restrictions had eased, the client travelled down to Redditch for more detailed test work on the SSSC Magnetic Separator in Bunting’s Recycling Test Facility. The tests successfully demonstrated the separation and recovery of fragmented stainless steel from different size fractions.
- Additional information: Recycling Test Facility
Following the positive test results, Bunting agreed to loan a 900mm wide SSSC Magnetic Separator for more tests onsite. During a further extensive period of testing, the metal recycling company determined the optimum performance and separation criteria including the ideal particle size range and matching capacity per metre width.
Subsequently, the UK-based metal recycling company has ordered two (2) SSSC Magnetic Separators with feed widths of 900mm and 1800mm. Both units are supplied with vibratory feeders, which control and regulate the flow of material. The 900mm wide unit is for processing the -50mm fraction, whilst the unit with the 1800mm feed width is for the larger sized fraction of +50mm to 200mm.
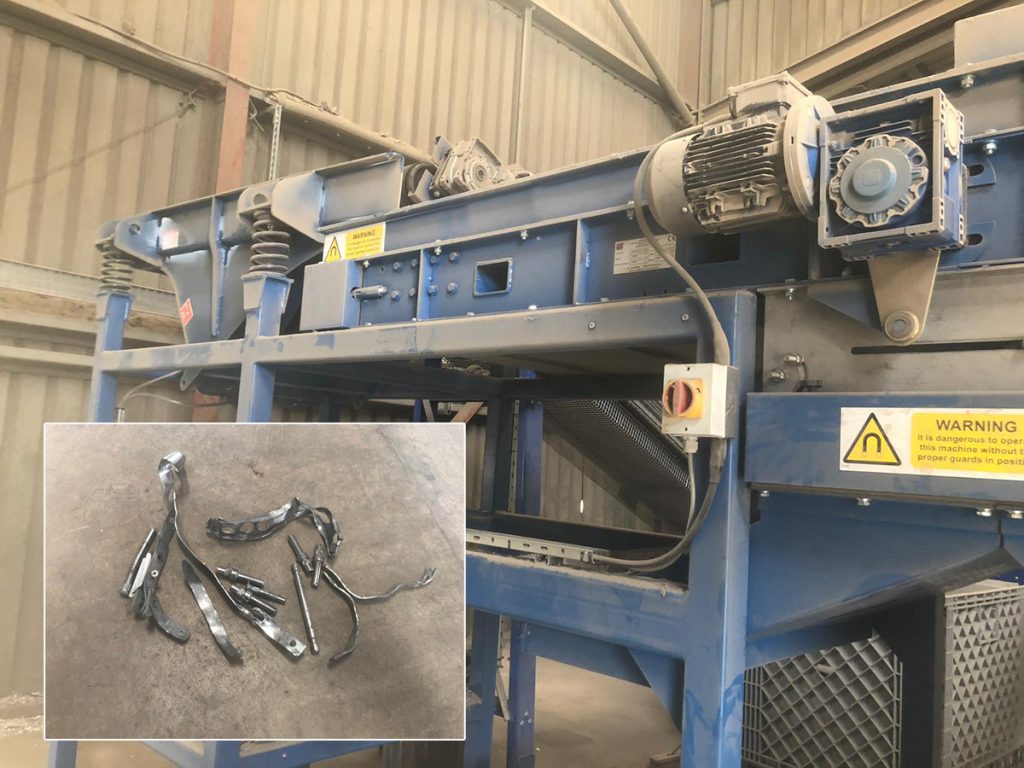
The SSSC (Stainless Steel Separation Conveyor)
The Stainless-Steel Magnetic Separator is unique. Bunting engineers designed a patented Neodymium Rare Earth magnetic roll that produces an ultra-strong magnetic force to attract even the weakest magnetic materials. The strength of the magnetic field is far greater than standard magnetic separators, extending the separation capabilities from just removing ferrous and strongly magnetic materials to materials that have a very low magnetic susceptibility.
- Technical product information: Stainless Steel Separators (SSSC and HISC)
The SSSC Magnetic Separator is a dual-pulley conveyor with a high-strength patented magnetic head roll. Material is fed onto the conveyor and transferred into the strong magnetic field. Weakly magnetic metals, such as fragmented stainless steel, are attracted and separated from unaffected non-magnetic materials.
Enhancing Metal Recovery
The addition of the SSSC Magnetic Separators to the existing secondary metal process further expands the company’s ability to maximise recovery and reduce waste.
“From the start, we worked very closely with the client,” explained Tom Higginbottom, Bunting’s External Sales Engineer for the North of the UK. “We know the strength of our SSSC magnetic rotor and the potential metal recovery. However, the metal recycling company knew their material and selected the best mix of frag, with the optimum particle size, for processing on the SSSC. By working together, we identified the metal separation capabilities and this resulted in the order of two units.”
The onsite tests on the 900mm wide SSSC resulted in the purchase of the production-size test unit. Manufacturing of the second 1800mm wide SSSC Magnetic Separator is presently taking place at Bunting’s Redditch plant.
The SSSC Magnetic Separator is part of the range of ferrous and non-ferrous metal separation systems designed and manufactured by Bunting. The SSSC is commonly installed as part of a three-stage metal separation system:
- Stage One: The removal of strongly magnetic metals typically with an Overband Magnet and Drum Magnet;
- Stage Two: The recovery of non-ferrous metal using an Eddy Current Separator;
- Stage Three: Fragmented stainless steel recovery;
Recycling Related Articles
For additional information on the SSSC Magnetic Separator for stainless steel separation or other metal separators (including Eddy Current Separators, Overband Magnets and other magnetic separators), please contact us on:
Email: Gordon Kerr at GKerr@buntingmagnetics.com
Telephone: +44 (0) 1527 65858
Follow us on social media