Magnetic Separator Air-Gap Explained
By Paul Fears | 14 February 2022
The ‘Air Gap’ plays a key role in the performance of a Magnetic Separator. In all magnetic separators, there is a gap between the magnet material or electromagnetic coil and the targeted particle. This ‘air-gap’ could be actual air or a non-metallic material such as stainless-steel or a rubber belt.
When assessing an application, our engineers carefully consider the relationship between the air gap and the magnetic force imparted on the particle to be separated.
Air Gaps and Magnetic Separation Equipment
The space between the actual magnet (permanent or electro) of a magnetic separator and the ferrous metal particle requiring separation is also known as the ‘air gap’. The maximum level of the magnetic field is found on the surface of a magnet in a magnetic separator, with that force reducing as a function of distance. Therefore, it is ideal to minimise the ‘air-gap’ (i.e. the distance between the magnet and the targeted separated metal) to maximise separation performance.
The ‘air-gap’ is particular to a magnetic separator design.
Tube or Cartridge Magnets
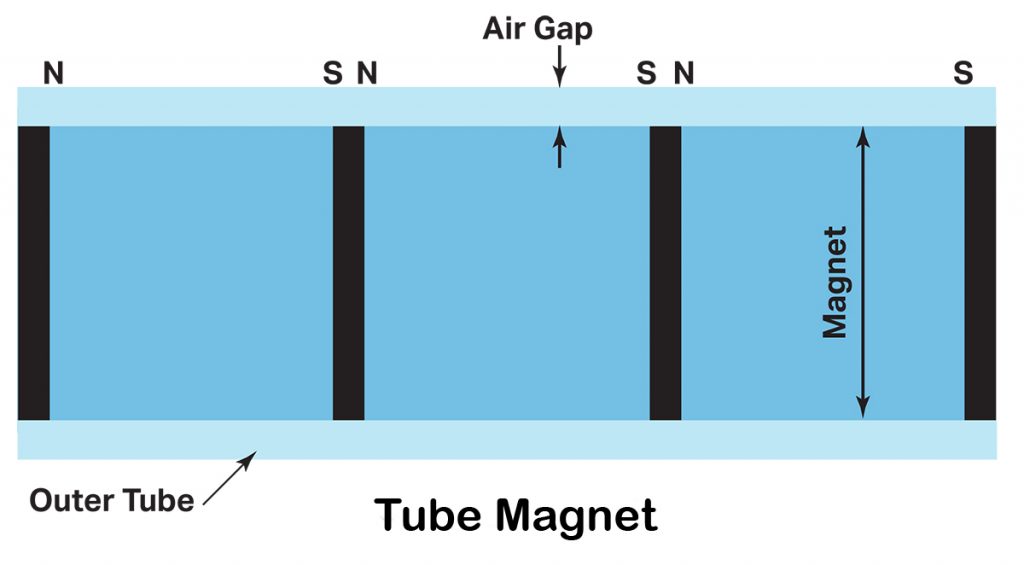
A Tube or Cartridge Magnet has permanent magnet slugs (approximately 25.4mm diameter ferrite or rare earth) housed inside a stainless steel sleeve. In a process, material flows over the surface of the Tube Magnet and so the only ‘air-gap’ is the thickness of the outer sleeve. In theory, the thinnest sleeve is optimum, but in practice, extremely thin stainless-steel sleeves wear quickly, causing failure of the Tube Magnet.
Tube Magnets are commonly used in Grid Magnet configurations. In such a design, there is careful consideration of the ‘air gap’ between the Tube Magnet surfaces as too wide a gap would result in ferrous metal passing through the grid without being captured. To ensure material passes over the surface of a Tube Magnet, deflectors are fitted above the gap between the Tube Magnets. This significantly reduces the risk of tramp ferrous passing uncaptured through the Grid Magnet.
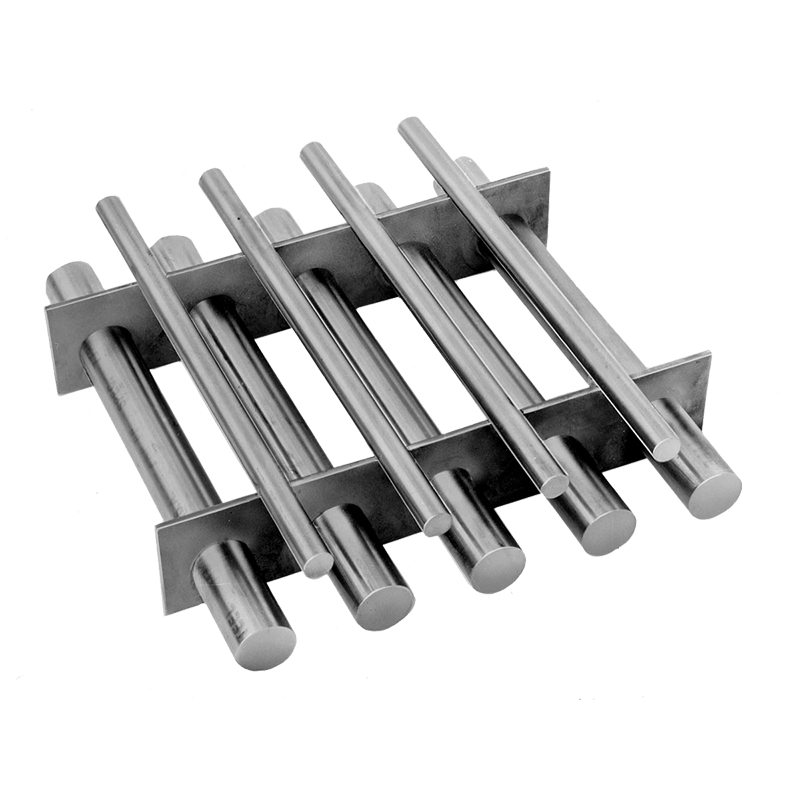
Another consideration for Tube Magnets is when processed material has a tendency to stick to and build up on the surface. This creates a secondary ‘air gap’. As this material ‘air gap’ increases, the magnetic strength and effectiveness of the Tube Magnet falls;
- Technical product details: Tube & Grid Magnets
Magnetic Head Pulley
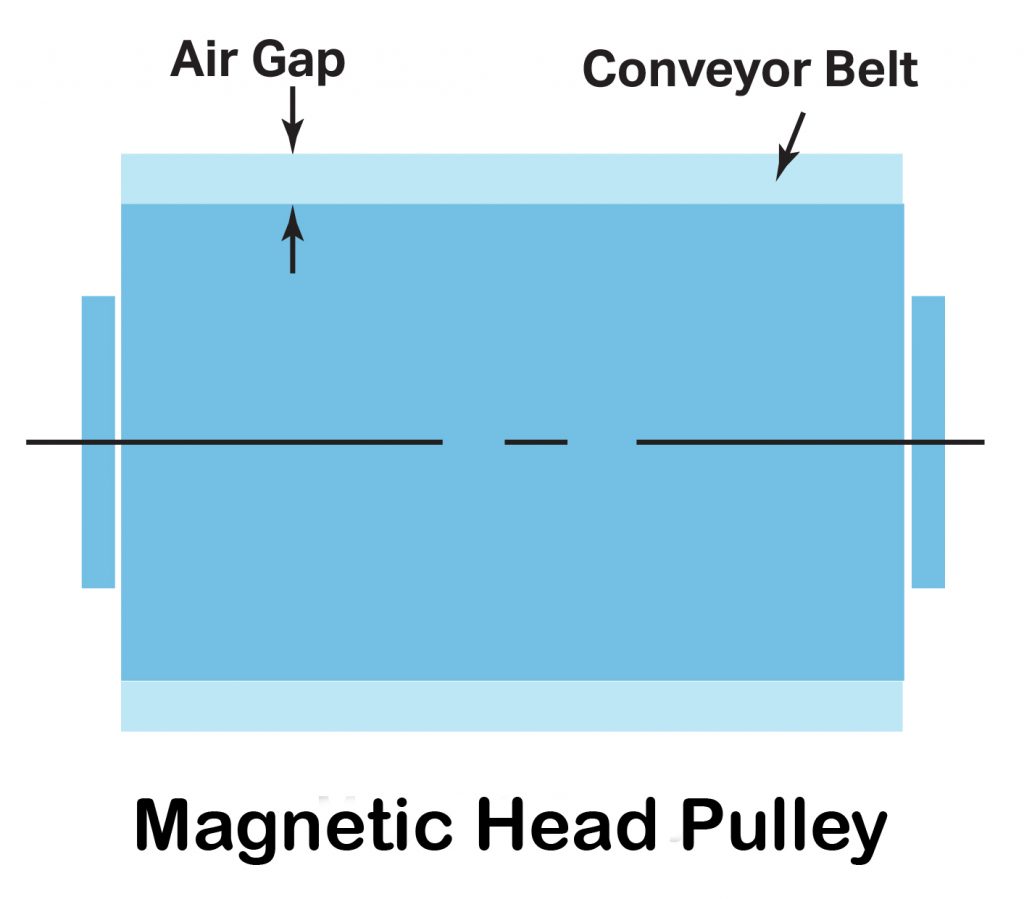
Magnetic Head Pulleys are very similar to Tube Magnets, although significantly larger (diameters start at a nominal 200mm and increase to over 1.5m), with a permanent or electromagnet housed inside a stainless-steel shell.
Magnetic Head Pulleys replace non-magnetic head pulleys to automatically remove tramp metal from conveyed materials. In a Magnetic Head Pulley, the ‘air gap’ consists of the stainless-steel shell, the transportation conveyor belt and the conveyed non-metallic material between the belt and the tramp ferrous metal.
- Technical product details: Magnetic Head Pulley
Drum Magnets
A Drum Magnet features a stationary magnet element housed inside a rotating non-metallic shell. In operation, the material is fed onto the surface of the Drum Magnet, commonly via a vibratory feeder. The ‘air-gap’ in a Drum Magnet is the internal distance between the magnet element and the inside of the outer shell (which is air) and the thickness of the non-metallic shell.
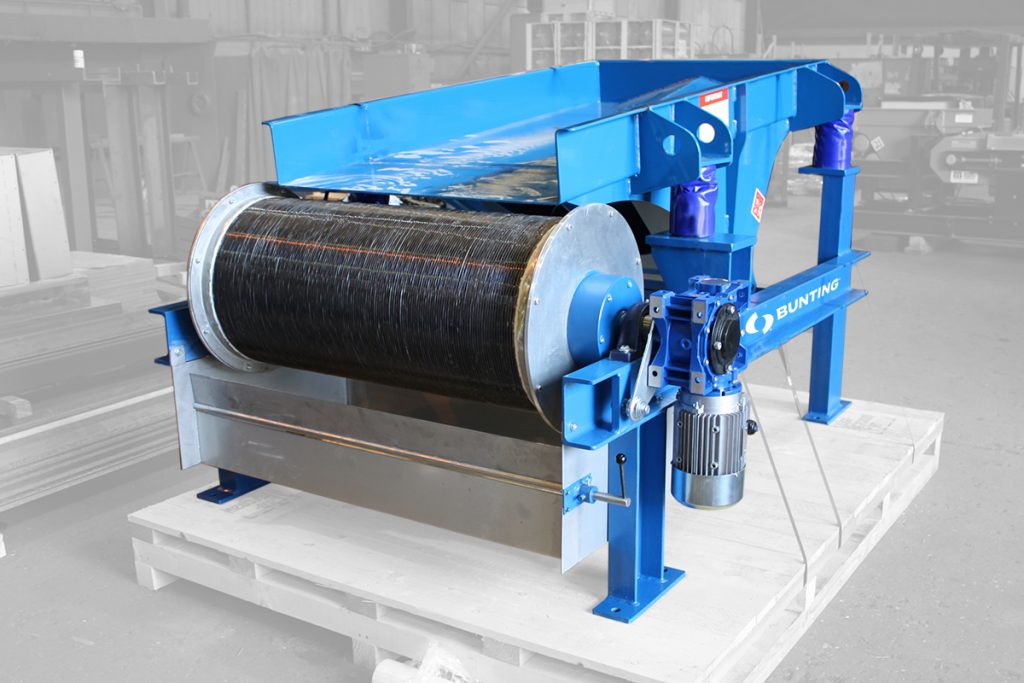
The magnetic field of a Drum Magnet (on the surface of the shell) is higher than that of a Pulley Magnet (on the surface of the conveyor belt) due to the thickness of the rubber transportation belt. Therefore, the Drum Magnet suits more difficult applications where the particles requiring separation are less magnetic.
- Technical product details: Permanent Drum Magnets
- Technical product details: Electro Drum Magnets
Suspended Magnets including Overbands
When a magnetic separator is suspended over a conveyor, the ‘air gap’ is the distance from the magnet face to the top and bottom of the transported material. As this ‘air gap’ increases, the magnetic field strength weakens and the ability to attract ferrous metal components reduces.
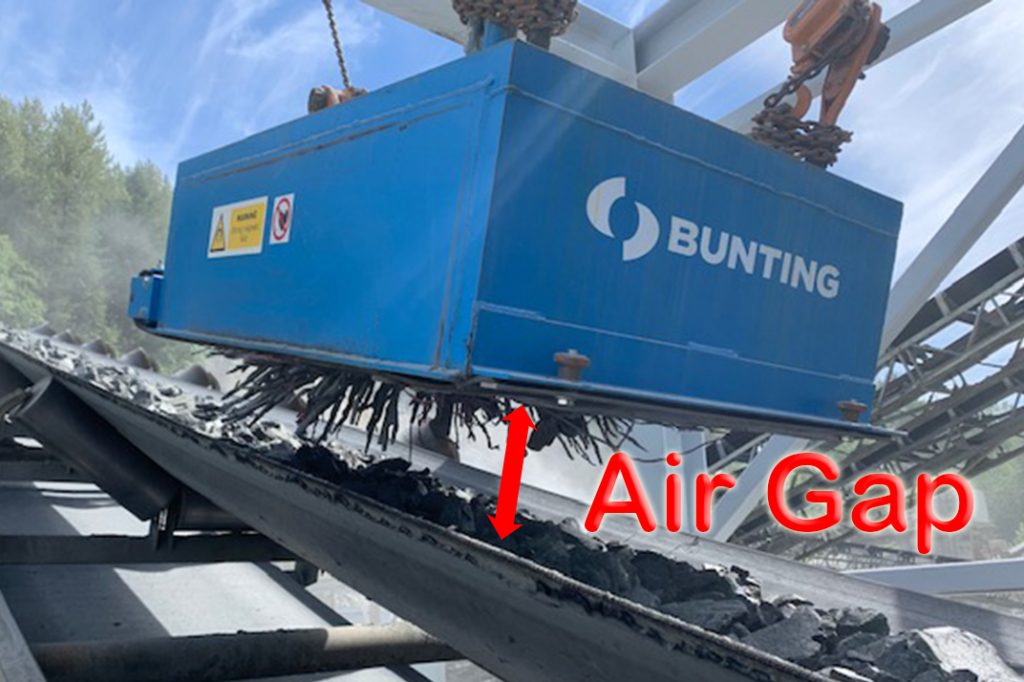
It is possible to position beltless Suspension Magnets and Plate Magnets close to the top of the burden, thus reducing the ‘air gap’. However, Overband Magnets have slatted belts to automatically transfer captured ferrous metal away from the magnet and product and into a separate collection area. This belt has a degree of sagging, which means that the suspension height (i.e., ‘air-gap’) has to be higher to prevent being hit by conveyed product.
Bunting’s application engineers assess the ‘air gap’ when selecting a Suspension Magnet or Overband Magnet. The suspension height is dictated by the burden depth, conveyor belt troughing angle, and conveyor belt speed. By using a bespoke design programme, Bunting’s engineers determine the amount of magnetic field projected by the Suspension or Overband Magnet at key points within the burden (i.e. on the top, in the middle and on the surface of the rubber belt). On determining the magnetic force required to lift and separate a specific size and shape of tramp ferrous metal, the optimum model of Suspension or Overband Magnet is selected.
- Technical product details: Suspension Magnets
- Technical product details: Overband Magnets
High-Intensity Magnetic Separators
High-intensity, Rare Earth Magnetic Separators such as the Rare Earth Roll Separator (RE Roll), High-Intensity Separation Conveyor (HISC) and Stainless-Steel Separation Conveyor (SSSC) feature ultra-strong magnetic rolls with very shallow fields.
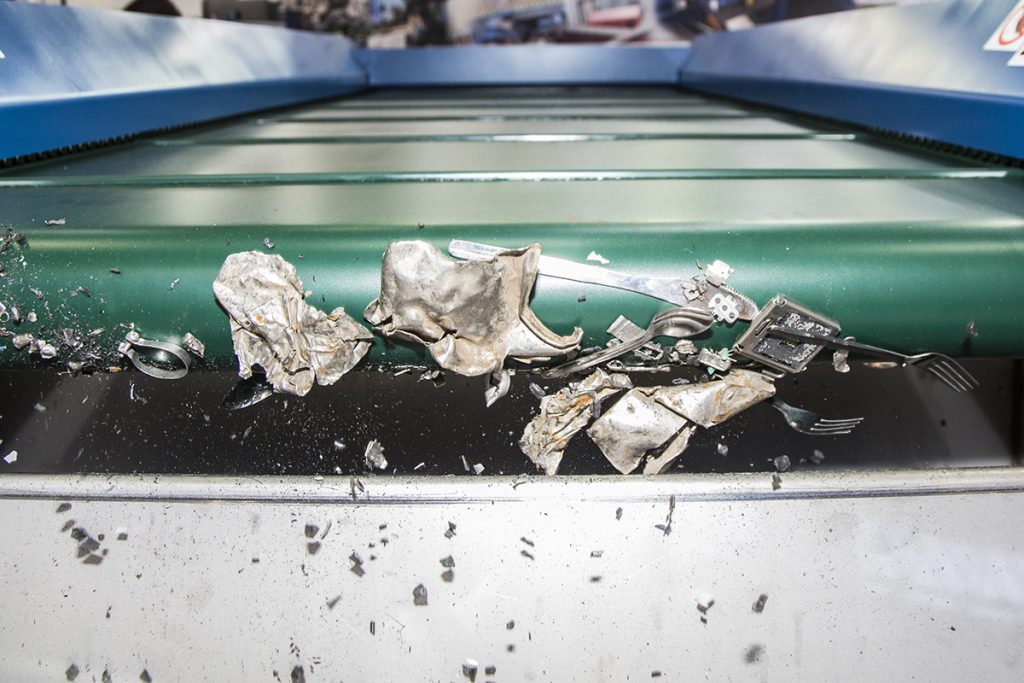
The high-intensity magnetic roll design features bare and unsheathed magnets and pole pieces. The only ‘air-gap’ is the thin conveyor belt used to transport a mono-layer of material into the separation zone. The depth of magnetic field produced by the magnet roll and the force needed to separate very weakly magnetic materials dictate the belt thickness. However, consideration is needed for potential wear as thinner belts are less resistant to damage from rogue ferrous metal contamination.
- Technical product details: Rare Earth Roll Magnetic Separator
- Technical product details: SSSC and HISC Stainless Steel Magnetic Separators
Related Technical Articles
For further information on Magnetic Separators or to discuss a specific project, including arranging a site visit, please contact our technical sales team on:
Email: Gordon Kerr at GKerr@buntingmagnetics.com
Telephone: +44 (0) 1527 65858
Follow us on social media