30 Year Magnetic Separator Market Evolution
By Paul Fears | 21 February 2022
Our Press Officer, Paul Fears, first became involved in marketing magnetic separators in 1989. In this blog, Paul looks back at the evolution of the magnetic separator market.
When I started my career in 1989, I had no comprehension of the importance of magnetic separators. I quickly discovered that the technology was used in every sector of the processing industry, from recycling to food production to the processing of minerals. Magnetic separators are essential for recovering metals from waste and secondary materials, protecting crushers in underground gold mines, and ensuring our food is ferrous-metal-free. They range from a Tube Magnet just 150mm long to a 13-tonne Electro Overband Magnet.
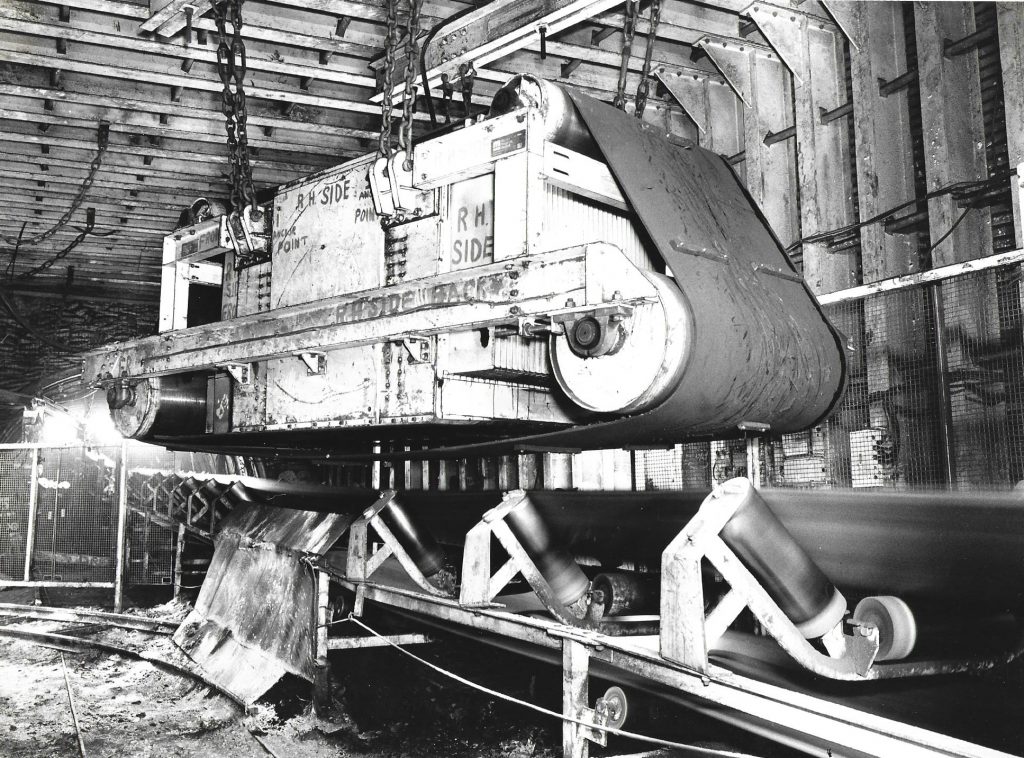
The market for magnetic separators has changed dramatically since 1989. At the time, British Coal still existed and was investing heavily in developing deep mine reserves. This included purchasing large and specialist Suspension and Overband Magnets for installation underground, of which supply was shared between the three major UK-based magnetic separators of the time. The magnets sat over conveyors transporting coal, attracting and removing any tramp ferrous metal (e.g., pit props, bolts, etc) to prevent damage to crushers, screens and other processing plant. However, as deep mine coal production in the UK fell (73,000 tonnes in 1990 to just over 35,000 by 1995), so did the demand for these large magnetic separators.
- Technical product details: Overband Magnets
Equipment sales to the coal sector moved from the UK to overseas markets, especially Russia and China. In those territories, the volume of mined coal was substantially higher than in the UK resulting in orders for multiple large Suspension and Overband Magnets. Many of these were bespoke, designed by UK-based engineers to separate even small ferrous blasting caps from heavy burdens of mined coal.
However, as the world moves away from fossil fuels such as coal, the demand for such specialist magnetic separators has fallen. Although coal remains a valued fuel in many developing countries, there is global pressure to reduce this reliance and move to environmentally-friendly and sustainable energy production.
Recycling Industry Magnetic Separator Demand
The demise of British Coal in the early 1990s coincided with the birth of the modern recycling sector. Secondary metal recycling companies such as the Bird Group and Mayer Parry were already successfully operating large automobile recycling plants across the UK. However, the early 1990s saw the rise of material recycling facilities (MRFs) and a focus on the recycling of household waste.
At the same time, several magnetic separator companies developed Eddy Current Separators. This magnetic-based technology enabled the separation and recovery of non-ferrous metals such as aluminium, copper and zinc. The first Eddy Current Separator, developed by the UK-based metal recycler Bird Group in 1981, was so significant that the company was presented with the Prince of Wales’ Award for Technology and Innovation and the Tomorrow’s World Award to Technological Development and Innovation. However, the electromagnetic technology was very expensive to purchase and operate, limiting use in a wider recycling environment.
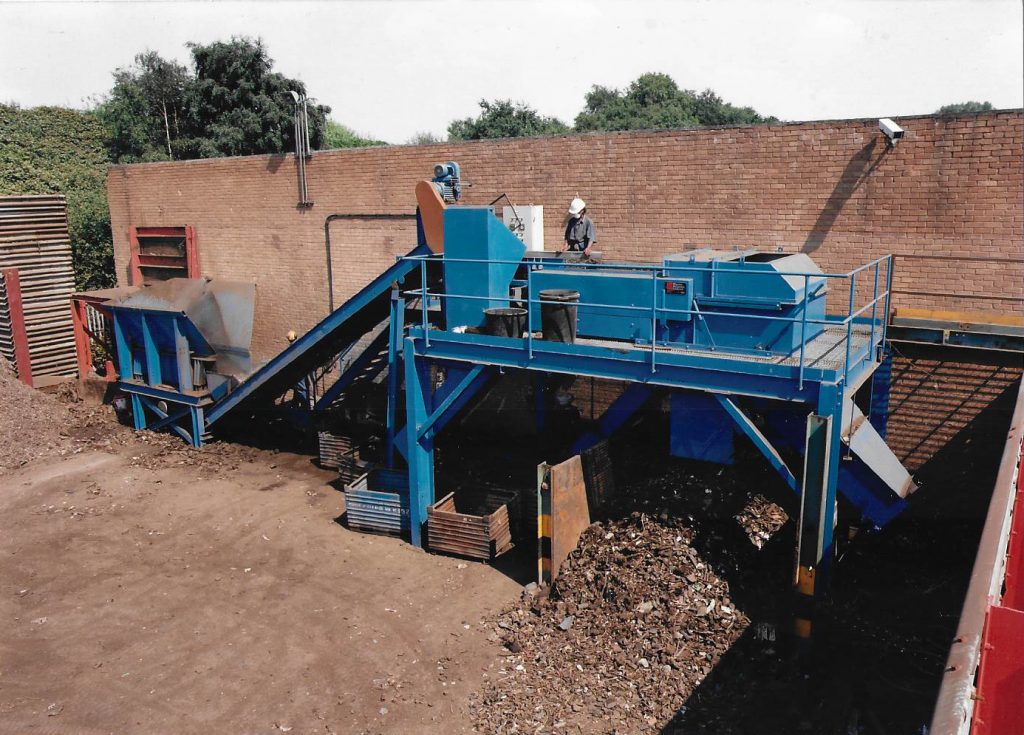
The Eddy Current Separators launched in the early 1990s used permanent, high-strength rare earth neodymium magnets to generate the magnetic force. The magnets are fixed to a carrier, in an alternating pole configuration, to form a rotor. This magnet rotor spins independently inside a non-metallic shell, reaching speeds of around 2500 RPM. A conveyor belt runs over the surface of the outer non-metallic shell and conveys material into the separation zone.
- Technical product details: Eddy Current Separators
When entering the high-speed, alternating, rotating magnetic field, a current is induced into the non-ferrous metal particle. This current creates a magnetic field, which is always in opposition to the magnet rotor, causing the physical ejection of the non-ferrous metal particle away from other non-metallic materials.
The permanent magnet design of the Eddy Current Separator significantly reduced the capital cost, providing a compact, low-energy and easy-to-use metal separator. For metal recyclers, the new Eddy Current Separators meant reducing the emphasis on metal separation processes such as heavy media, whilst opening up new waste management opportunities. Through the decade, Eddy Current Separator sales grew, not only due to the demand from metal recyclers but also companies designing, installing and operating MRFs. The relatively easy recovery of valuable aluminium beverage cans proved an important revenue source in the United Kingdom, especially with the opening of the Alcan (now Novelis) Warrington can recycling plant in 1991.
Eddy Current Separator design continues to evolve with an ever-increasing demand. The successful widening of waste recycling capabilities requires enhanced material separation, including the recovery and removal of both ferrous and non-ferrous metals.
The Neodymium Magnet Effect
The development of the permanent neodymium (NdFeB) magnet by General Motors and Sumitomo Special Metals in 1984 dramatically changed the magnetic separator market, enabling the birth of technology such as the Eddy Current Separator. By 1989, neodymium magnets featured in many high-intensity magnetic separators from simple Tube Magnets to more complex Rare Earth Roll Magnetic Separators.
Basic magnetic separators designs, such as Tube Magnets and Plate Magnets, had traditionally used low-strength ferrite magnets. With the wider availability of rare earth NdFeB, these magnetic separators became significantly stronger as well as lighter and smaller. Many food retail outlets and producers, such as Marks & Spencer in the United Kingdom, instructed all suppliers to fit rare earth magnetic separators into their food manufacturing processes to capture even the smallest and weakest metal contamination. The introduction of NdFeB sparked a new demand for magnetic separators, especially with the replacement of many older lower strength versions.
Purification of Non-Metallic Minerals
As a qualified geologist, in the early 1990s, I became responsible for developing business in the mineral processing and ceramics sectors. The development of high-intensity, neodymium magnetic separators was of huge importance to the non-metallic minerals industry. Non-metallic mineral producers use high-intensity magnetic separators to purify minerals such as feldspar and silica sand, which are used in the manufacture of ceramics and glass. With the development of Rare Earth Roll Magnetic Separators, using discs of neodymium sandwiched between steel poles in a roll, mineral processors had a low-energy but high-intensity magnetic separator alternative to traditional electromagnetic equipment such as the Induced Magnetic Roll Separator.
- Technical product details: Rare Earth Roll Magnetic Separator
The Rare Earth Roll Separator is a twin pulley conveyor with a single high-intensity NdFeB head roll. A mono-layer of minerals, transported on a very thin belt, move into the high-intensity magnetic field of the head roll. Strongly magnetic minerals are held and deposited underneath the roll, with weakly magnetic minerals deflected from a normal trajectory and separated with strategically placed splitters.
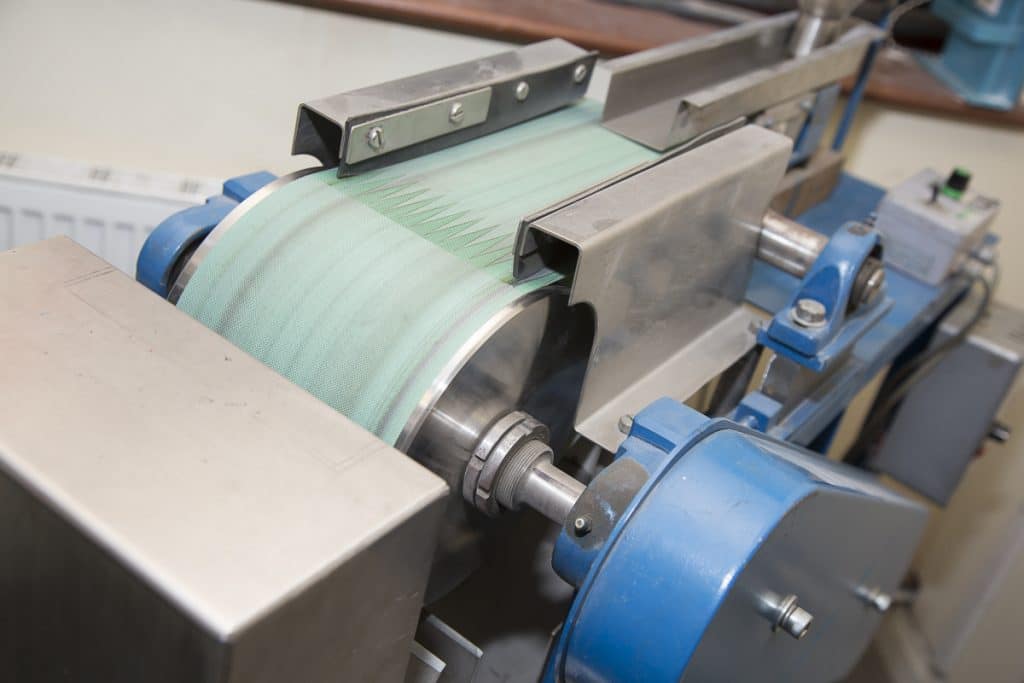
The Rare Earth Roll Separator was compact as well as easier to install and operate. This meant that mineral processors could install multiple banks of Rare Earth Roll Separators and produce non-metallic minerals that were exceptionally pure and magnetic mineral free.
In more recent times, as the purest mineral deposits reach the end of their life, mineral processors are using high-intensity magnetic separators to rework mineral waste and process previously unmanageable reserves. The process is often more complex with higher levels of contamination, sparking a renewed demand for high-intensity magnetic separators.
Recent Magnetic Separator Development
The needs of material processors have driven the development of magnetic separators. In recent years, the SSSC and HISC ultra high-intensity magnetic separators enable metal recyclers to recover fragmented stainless-steel. When recycling plastic waste and other secondary materials, this magnetically powerful technology removes small problematic metal contamination previously inseparable, whilst also recovering valuable and previously unrecoverable stainless-steel.
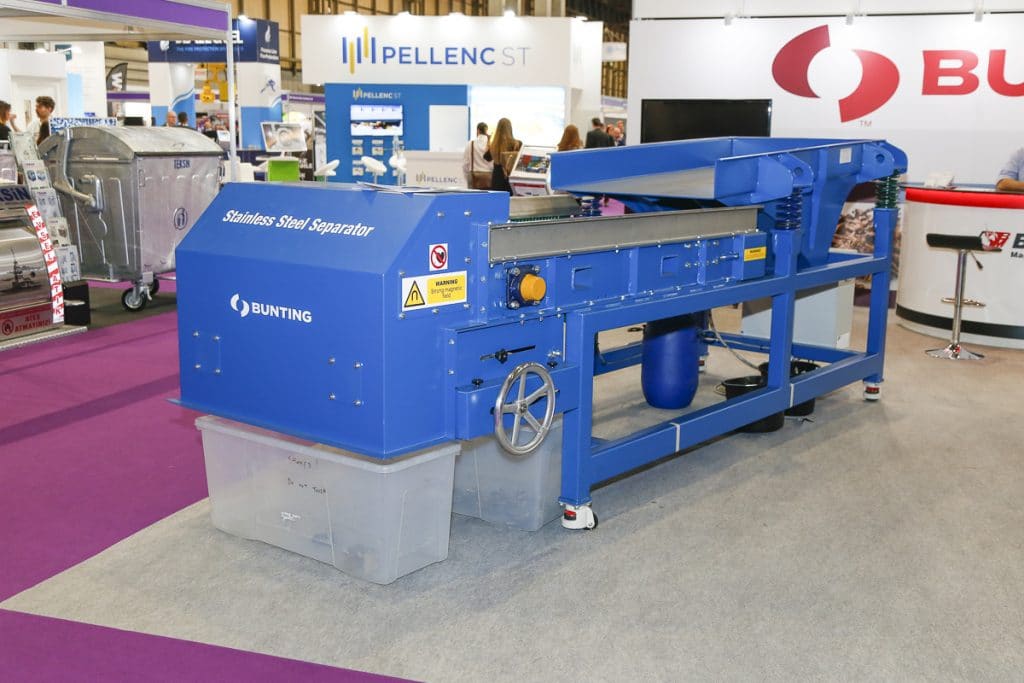
Both the SSSC and HISC operate in a similar way to the Rare Earth Roll Magnetic Separator, with the ultra-high-intensity magnetic roll at the head of a conveyor belt. Material on the belt moves into the magnetic field, where weakly magnetic particles are attracted and held before being deposited underneath in a separate collection area.
- Technical product details: Stainless Steel Separators
The Future for Magnetic Separation
In 1989, I could not have predicted the evolution of the magnetic separator market. The importance of technology has never been greater, enabling the vital recycling of waste and the development of precious mineral reserves. Advances in magnet technology will create increasingly stronger magnetic separators and open up new, presently unknown, applications. Despite often being hidden away from sight, magnetic separators are one of the most important processing technologies of all.
Related Technical Articles
For further information on Magnetic Separators or to discuss a specific project, including arranging a site visit, please contact our technical sales team on:
Email: Gordon Kerr at GKerr@buntingmagnetics.com
Telephone: +44 (0) 1527 65858
Follow us on social media