Separation Technology Training for Chemical Engineering Students
By Paul Fears | 14 December 2021
During a specially arranged training day, Bunting demonstrated state-of-the-art separation technology to a group of 2nd-year Chemical Engineering students from the University of Birmingham. The event was the first of two seminars arranged for industrial-focused students studying at the university. The training days took place at Bunting’s Customer Experience Centre in Redditch, just outside Birmingham in the UK.
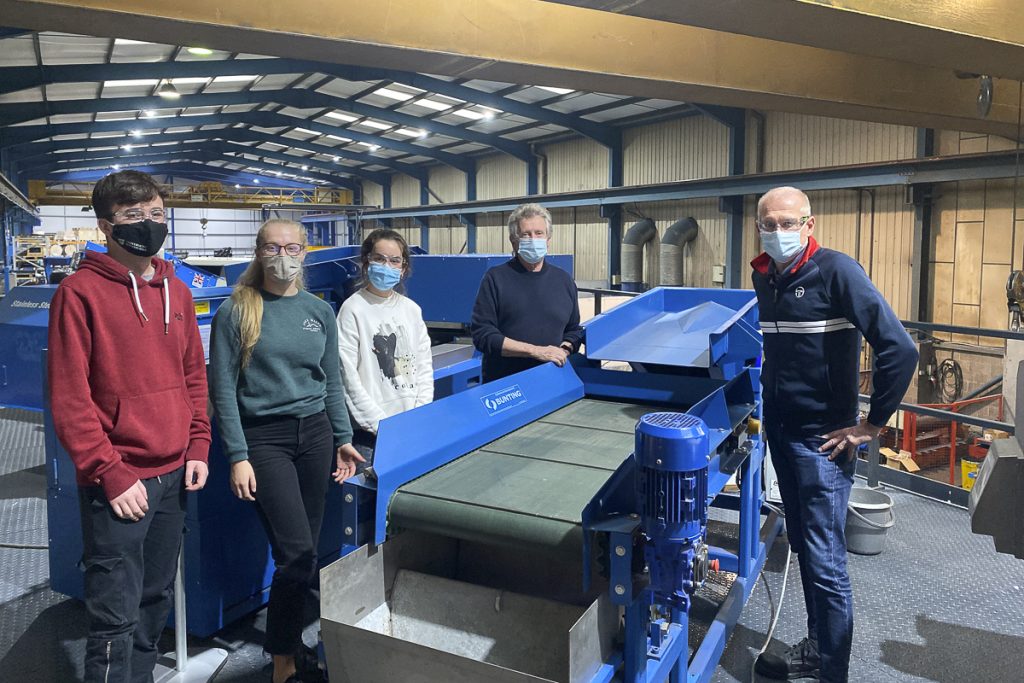
On the chemical engineering course, students can elect to visit a local company to see engineering in action. Six students took part in the first of the two training days, with the second taking place in early 2022.
The training sessions were overseen by Bunting’s Laboratory Manager, Neil Rowson, and Technical Sales Manager, Phil Tree. Both Neil and Phil have decades of experience in magnetic separation, with Neil also being a key member of the ElectroStatic Separator development team.
The training day began with a short introduction to Bunting, before progressing onto the principles behind physical separation techniques for minerals and recycling. This included reviewing material separation on a range of high-intensity magnetic separators. After a short lunch, the students were split into two groups.
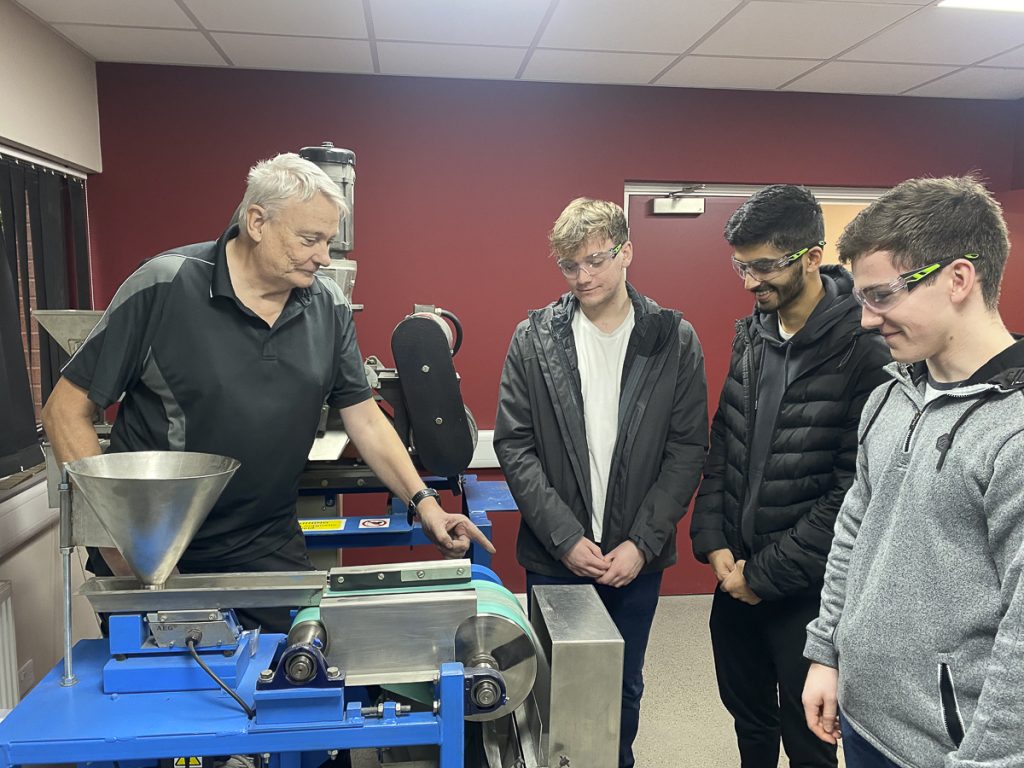
Group A focused on mineral separation in the mineral-focused test laboratory. Neil demonstrated the Hitachi High-Tech X-MET8000 handheld X-ray Fluorescence (XRF) analyser and representative sampling for accurate analysis. This was followed by the concentration of ilmenite for titanium production by processing beach sands on a Magnetic Disc Separator. Titanium has a wide range of applications as white pigment and is used in steel as an alloying element (ferro-titanium).
- Technical product information: Magnetic Disc Separator
The mineral testing continued with the demonstration of mica being removed from crushed granite to produce a clean feldspar using the Rare Earth Roll Magnetic Separator. Feldspar is used in a wide range of industries such as glass and ceramics manufacture.
- Technical product information: Rare Earth Roll Magnetic Separator
After the focus on dry separation, Neil introduced the concept of wet high-intensity magnetic separation, showing the removal of paramagnetic minerals from calcium carbonate.
Bunting’s mineral testing laboratory is equipped with a wide range of separators including a hydro cyclone, which Neil used to demonstrate the removal of coarse minerals from fine minerals. The sample tested was a rare earth mineral deposit from Canada for a project Bunting is working on with McGill University in Montreal, Quebec.
With Group B, Phil focused on recycling. Bunting’s extensive range of magnetic separators enables the recovery and separation of small to large ferrous and non-ferrous metals. The first demonstration showed how ultra-strong magnetic forces enable the separation of fragmented stainless steel on the patented High-Intensity Separation Conveyor (HISC) and Stainless-Steel Separation Conveyor (SSSC).
- Technical product information: Stainless Steel Magnetic Separators
Eddy Current Separators feature in many recycling plants to recover or remove non-ferrous metals from non-metallics. Since the first developments in the early 1990s, design modifications have enhanced the separation capabilities to separate increasingly smaller non-ferrous metals. Phil demonstrated the technology, explaining the unusual physics behind a separation that involves a high-speed, high-strength rotating magnet rotor physically ejecting non-ferrous metals away from non-metallics.
- Technical product information: Eddy Current Separators
After the material test demonstrations, Phil gave both groups a factory tour, showing magnetic separators and metal detectors in manufacture and the technical office.
The day finished with a question-and-answer session.
“Material separation, both for developing important mineral reserves or for the recycling of materials, has never had greater importance,” explained Neil. “During the training day, we were able to show future engineers the separation technology of today and tomorrow. Understanding the separation behaviour of minerals and materials forms a key step in developing processes to maximise recovery and purity.”
Related Recycling Articles
For further information on Magnetic Separators, Eddy Current Separators, and ElectroStatic Separators or to discuss a specific project including undertaking tests in our Customer Experience Centre, please contact our technical sales team on:
Email: Gordon Kerr at GKerr@buntingmagnetics.com
Telephone: +44 (0) 1527 65858
Follow us on social media