Bunting-Redditch 2021 Review
By Paul Fears | 13 December 2021
Who would have thought, as we write this in December 2021, that the Covid-19 pandemic would still be headline news across the globe? In addition, since the summer of 2021, a global shortage of materials, staff shortages, and transport delays matched with rising prices have created new challenges for manufacturing companies.
Despite the background of doom and gloom, Bunting-Redditch has had a very successful 2021.
A Great Start to 2021
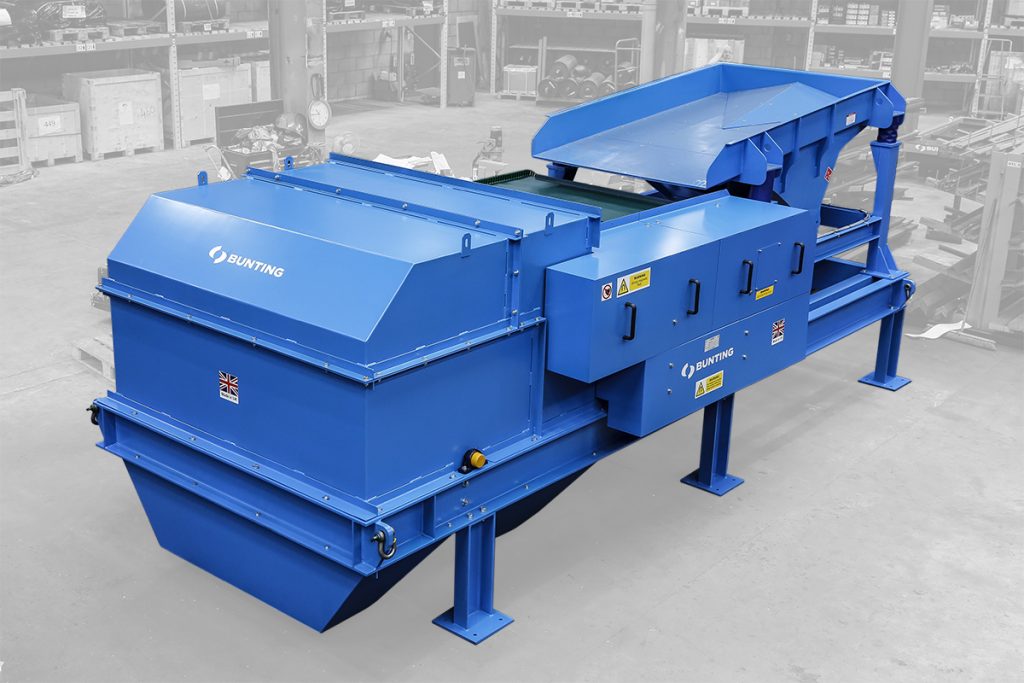
The year started with securing a major export order to supply one Eddy Current Separator and three ElectroMax Overband Magnets for an overseas construction and demolition waste management plant designed and built by CRS NI (Complete Recycling Systems). The separation equipment will recover both ferrous and non-ferrous metals. All the equipment left the UK in September for installation in the new plant.
The refurbishment of well-used and functional magnetic separators is a great way of recycling equipment. With a long history of supplying magnetic separators, we work with many companies on such refurbishments. In February, this included a 6-year old Electro Overband Magnet (model 155 OCW 45 CB) used to remove tramp ferrous metal from biomass pellets.
The continued and forecasted rise in the use of electric vehicles raises many recycling challenges including managing waste batteries. Bunting is working with the University of Birmingham in assessing physical separation techniques to separate very weakly magnetic particles, and, in April, supplied a laboratory-scale Rare Earth Roll Separator for their School of Metallurgy and Minerals research team.
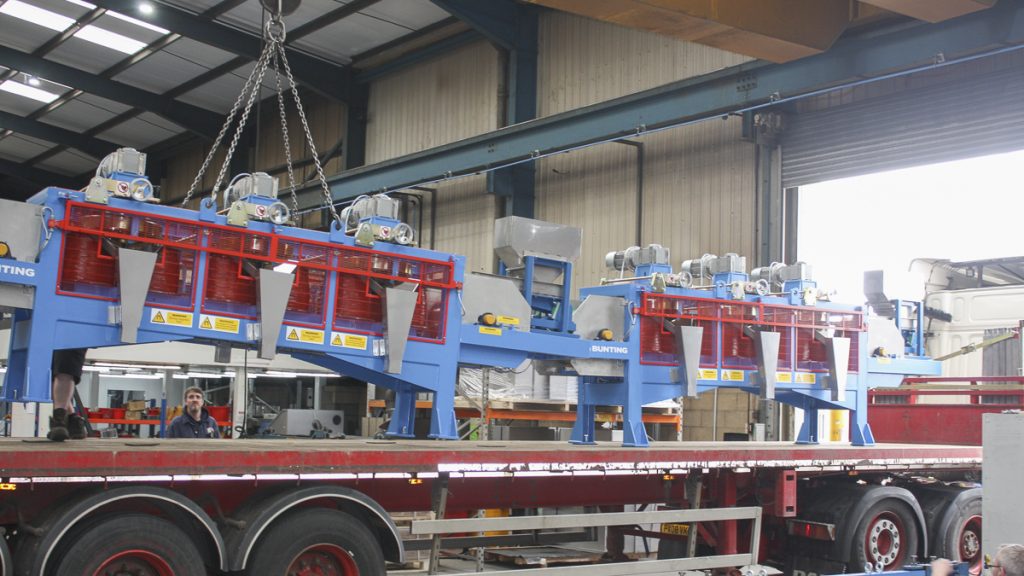
Coltan (columbite-tantalites) provides key raw materials used in mobile phones, personal computers, electronics, and superconducting materials. Following separation test work in the Bunting laboratory, a Nigerian Coltan processor ordered two Magnetic Disc Separators, which were despatched in April. The high-intensity magnetic separators enable the recovery of minerals with different magnetic susceptibilities.
Sales at the beginning of 2021 had been exceptionally strong, especially for recycling, mining, and mineral processing projects. Mobile Metal Separator producer Steelweld Enviro Products Ltd and CRJ Services ordered six sets of Eddy Current Separators and Rare Earth Drum Magnets in just three (3) months, highlighting the continued growing demand in the recycling sector.
This sales growth resulted in a new 43-year record order month (by value) in April, highlighting the rate of the recovery after a very difficult 2020.
Investing for the Future
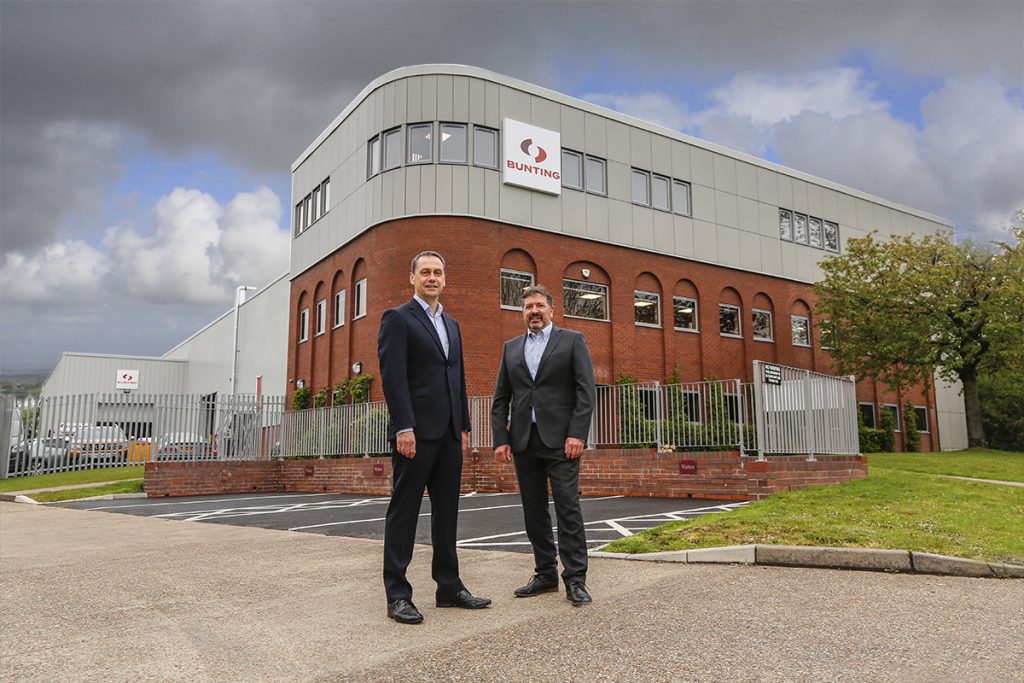
With such sales growth, the completion of the 12-month long extension work at Bunting’s Redditch facility was perfectly timed. Both the manufacturing and office space increased by 50%, along with the creation of a state-of-the-art Customer Experience Centre for material testing. The extension provided vital space to fulfil the growth in both domestic and overseas equipment orders.
The investment in the Redditch facility included the installation of a new powder coating plant. Powder-coated painting produces a top-quality finish and further enhances Bunting’s manufacturing standard.
The strong order activity continued into July with a UK-based toilet tissue, facial tissue, and kitchen towel manufacturer installing four (4) Bunting meTRON 07 CI Metal Detectors with integral conveyors. With the health and safety of customers and users being paramount, the new Metal Detectors identify any final packed products contaminated with metal prior to leaving the manufacturing plant.
September marked a welcome return to international exhibitions. Bunting exhibited at both RWM (the UK waste and recycling show) and Interplas (the UK plastic show) in the month. Later in the year, Bunting exhibited at the Ecomondo Green Technology Expo (Rimini, Italy in October) and E-Waste World Conference and Expo (Frankfurt, Germany in November). Although footfall was, as expected, down on pre-pandemic levels, the quality of leads at the shows was very high.
At Interplas, Bunting launched the Shredder Feeder Conveyor. Specifically designed for recycling plastics, both in-house regrind and from secondary sources, the Shredder Feeder Conveyor provides an even and controlled feed into a shredder or granulator whilst including either a magnetic separator or metal detector to protect a shredder or granulator from metal damage.
Educating Future Recycling Engineers
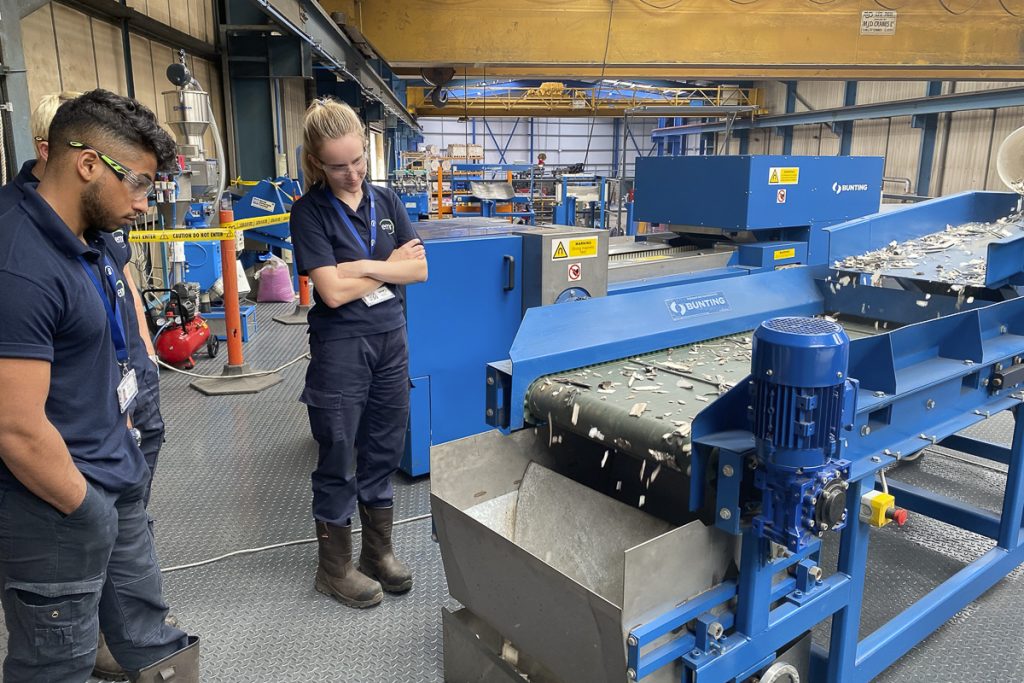
Bunting’s new Customer Experience Centre is an ideal training ground for future recycling engineers. Students, on a year’s work placement with European Metal Recycling (EMR), attended a training day in October at Bunting’s Redditch plant assessing the latest magnetic, eddy current and electrostatic separators. The training illustrated the importance of optimising material separation in the drive towards increasing secondary material recycling rates.
In recent years, Bunting has invested in developing overseas sales offices. The November appointment of Marcel Graef and 3SMI as the exclusive agent in Germany, Austria, and Switzerland added vast experience and knowledge. Marcel Graef’s has built a reputation as a leading expert in material separation, particularly with magnetic and eddy current technology.
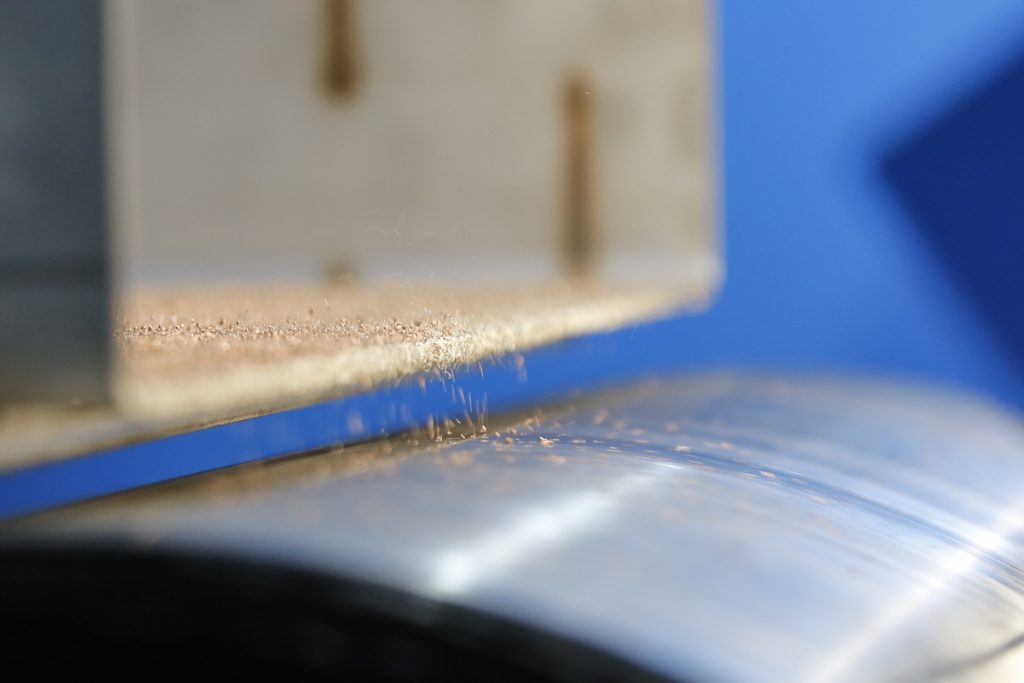
The successful recovery, recycling and reuse of secondary materials are dependent on technology such as the ElectroStatic Separator. Following the launch in late 2020, Bunting has designed, built and commissioned ElectroStatic Separators for companies recycling metals and plastics. In November, Bunting completed manufacturing of a 1m wide ElectroStatic Separator, the widest unit built to date. The team are presently undertaking tests on the ElectroStatic Separator for companies processing a wide range of waste materials with further orders expected early in 2022.
Research and development are essential to successfully manage waste. Cranfield University in the UK heads up TransFIRe (Transforming Foundation Industries Research and Innovation hub), developed in response to the Industrial Strategy Challenge Fund (ISCF) call to transform the foundation industries, namely: chemicals, cement, ceramics, glass, metals, and paper. In November, Bunting announced their involvement as a project partner, assisting with methods to successfully separate and recover metals.
“We [Bunting] have reached many milestones in 2021, providing a solid platform for further growth in 2022,” said Adrian Coleman, the General Manager of Bunting-Redditch. “With a modern manufacturing facility and world-leading Customer Experience Centre, we have the ability to provide our customers with unrivalled support. However, our success is all down to our excellent team at Redditch. They constantly adapted in the face of many challenges, including the Covid-19 pandemic. Both Simon [Ayling – Bunting’s European Managing Director] and I wish to thank them all. In 2022, we will continue to evolve and improve.”
Related Articles
For further information on Magnetic Separators, Eddy Current Separators, and ElectroStatic Separators for or to discuss a specific project, including undertaking tests in our Customer Experience Centre, please contact our technical sales team on:
Email: Gordon Kerr at GKerr@buntingmagnetics.com
Telephone: +44 (0) 1527 65858
Follow us on social media