The Crusher’s Arch Enemy – Tramp Metal
By Paul Fears | 29 March 2021
Crushing quarried aggregate is a key process stage of most quarries and when recycling demolition waste. Effectively protecting the crusher from rogue tramp metal damage prevents production losses and repair costs.
The wide range of available crushing technology enables the production of optimally sized aggregate. Whereas Jaw and Gyratory designs commonly feature as primary crushers, secondary stage crushing often involves Cone Crushers.
Whether primary or secondary, tramp metal entering the crusher causes significant and potentially catastrophic damage.
Resisting Tramp Metal Damage
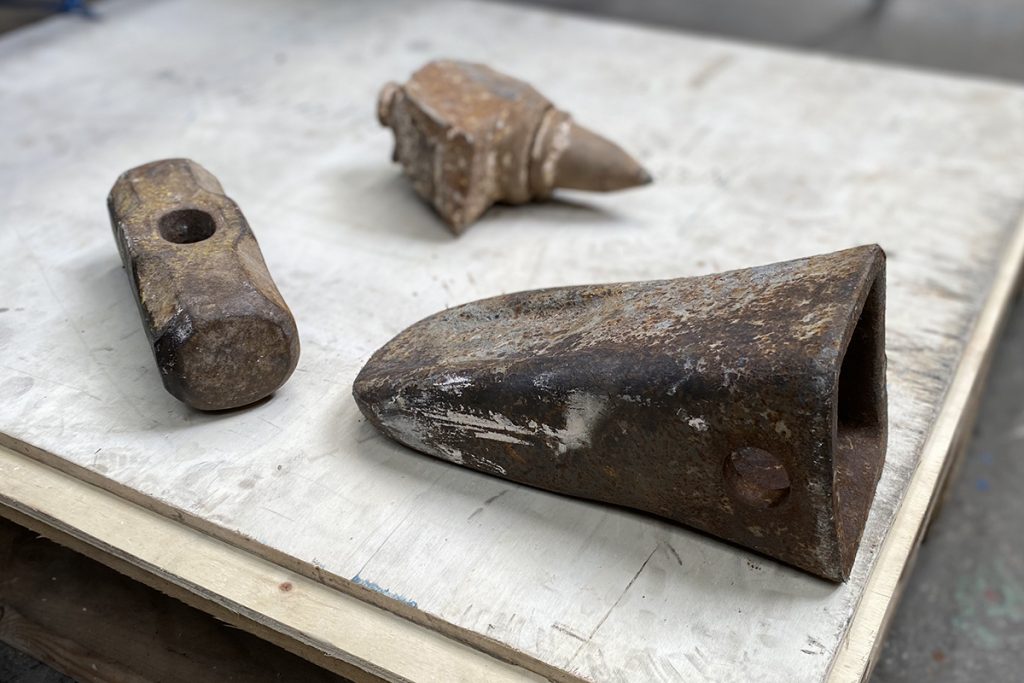
The definition of ‘tramp metal’ is any item of rogue metal not naturally present in the quarried aggregate. Such contamination includes digger teeth, pit props, blasting caps, nuts and bolts, and metal originating from the wear and tear of process plant. In demolition waste the most common tramp metal occurs as rebar, the reinforced steel rods used to strengthen concrete.
Tramp metal occurs as both ferrous and non-ferrous metal. Digger teeth are an example of non-ferrous tramp metal as they are constructed from manganese steel. Nuts and bolts, as well as rebar, is commonly ferrous.
There are two superheroes that confront and defeat the crusher’s arch enemy – Tramp Metal. Magnetic separators attract and remove ferrous metals, whilst Metal Detectors detect all metals.
Metal Detectors for Tramp Metal
A Metal Detector features a coil either mounted under-and-over or underneath a conveyor. The conveyed aggregate either passes through or over the detector. The detection of metal occurs through the disturbance of the magnetic field produced by the metal detector coil. Detection of the presence of tramp metal sends a signal to the remotely located control. On receiving the signal, the control either stops the conveyor and initiates an alarm; or sets off a diverter gate to reject a batch of material.
There are different Metal Detector designs to suit different tramp metal detection objectives.
TN77 Industrial Metal Detectors
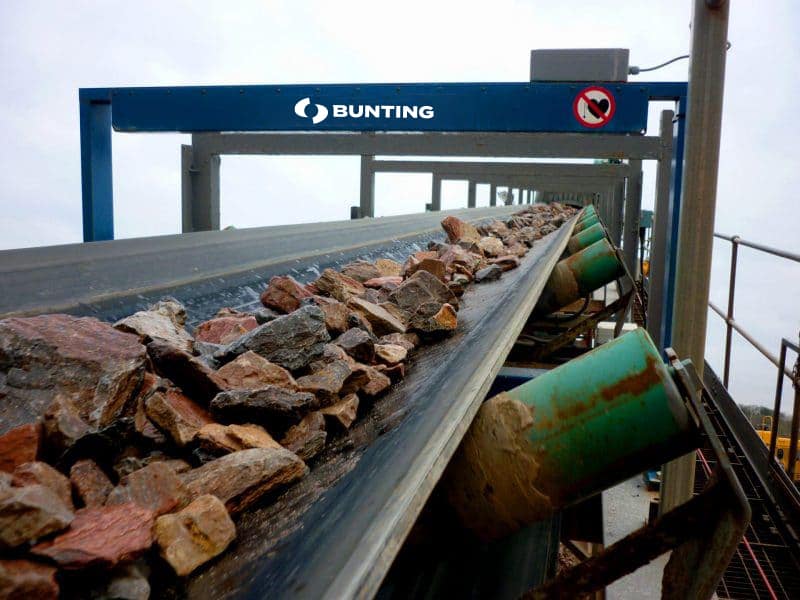
The tunnel-type TN77 Industrial Metal Detector provides a continuous inspection of any non-metallic or non-conductive material, identifying and locating problematic tramp iron and manganese steels. Unlike many other Metal Detectors, the TN77 is capable of indicating the simultaneous detection of 1 or 2 pieces of tramp metal. The Metal Detector also overlooks non-magnetic copper-alloy belt fasteners (present in many rubber conveyor belts), which may cause false ‘trips’.
- Technical Product Details: TN77 Metal Detectors
Magnetic Separators for Ferrous Tramp Metal
Magnetic Separators attract magnetically-susceptible tramp metal (e.g., steel and iron), automatically removing the problematic contamination from the aggregate and commonly work in prior to Metal Detectors. Removing the magnetic tramp ferrous (the majority of tramp metal), enables metal detectors to focus on the non-ferrous metals. Also, automatically removing tramp ferrous metal significantly reduces the number of times a metal detector stops a conveyor for the manual removal of tramp metal and, hence, improves productivity.
Selection of the optimum magnetic separator design for any given application is determined by the process and material specifications.
Overband and Suspension Magnets
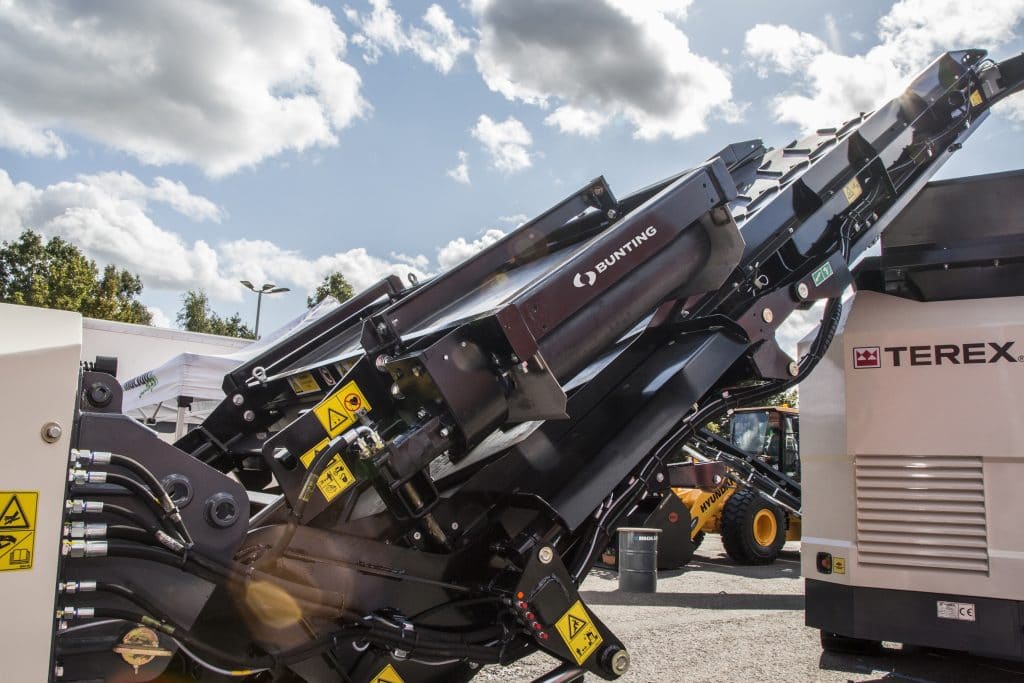
An Overband or Suspension Magnet is positioned over a conveyor, with tramp iron attracted up and out of the conveyed aggregate. The ‘Suspension’ design features a magnet block which requires the manual removal of separated metal from the magnet face, whilst the ‘Overband’ design includes a self-cleaning belt that automatically removes captured metal away and into a collection area.
The magnetic field is produced using an enclosed casing of carefully arranged permanent magnets or an electromagnetic coil wound around a steel core.
Permanent Overband and Suspension Magnets feature widely on mobile crushers and screens, especially for sites recycling demolition waste and quarries. Although some permanent Overband and Suspension Magnet designs operate at high suspension heights, the majority are suited for positioning at a maximum height of 300mm above the conveyor. Such permanent designs successfully separate larger longer tramp iron such as rebar.
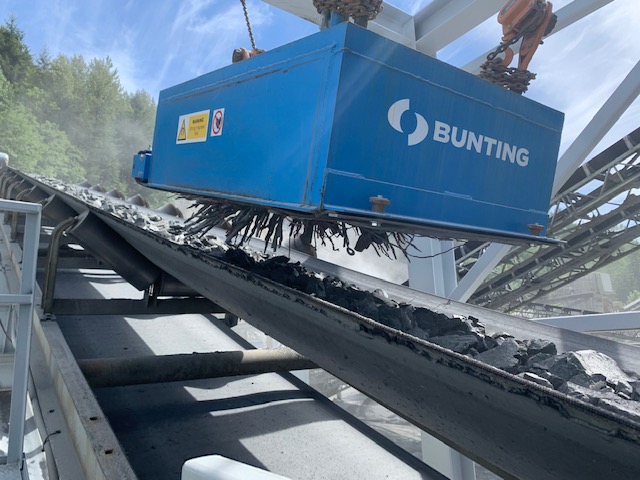
Quarry applications with higher capacities, using wider conveyors and with deeper aggregate burdens, are better suited to Electro Overband or Suspension Magnets, which generate a far deeper and stronger magnetic field than the permanent design.
The electromagnetic coil is either cooled with oil or air, with Bunting’s air-cooled ElectroMax model specifically designed as a compact and powerful option for installations where either weight or space is an issue.
- Technical Product Details: Overband Magnets
Magnetic Head Pulleys
The less commonly used Magnetic Head Pulley replaces the standard head pulley of a conveyor. In operation, any tramp iron present in the conveyed ore and reaching the end of the conveyor is attracted to the Magnetic Head Pulley and held onto the surface of the conveyor. As the returning conveyor leaves the under surface of the pulley, the separated tramp iron falls away under gravity into a designated collection area.
The Magnetic Head Pulley suits existing installations where space is limited, restricting the possibility of installing Overband or Suspension Magnets over conveyors.
- Technical Products Details: Magnetic Head Pulleys
Bespoke Engineered Solutions
Once again, tramp metal – the crusher’s arch enemy – is defeated by the superhero duo of the magnetic separator and metal detector. However, understanding the installation, the application and the process are all important when considering the optimum solution.
At Bunting’s Redditch manufacturing plant in the UK, the applications engineering team works closely with quarry engineers, contractors and designers before making any recommendations.
Relating Quarrying & Mining Articles
- Electro Overband Magnet Removes Metal from Copper Ore
- Large Electro Suspension Magnets at West Burton Power Station
- 10 Tonne Master Magnets Overbands Installed In Russian Coal Processing Plant
To discuss a specific project or for additional information on detecting and removing tramp metal from quarried aggregate or mined ore, please contact us on:
Email Gordon on: GKerr@BuntingMagnetics.com
Telephone: +44 (0) 1527 65858
Follow us on social media